Advantages of Ceramic Fiber Module Insulation for Molten Iron Ladle Cover
Table of Contents
1.Importance of Insulating the Molten Iron Ladle Cover
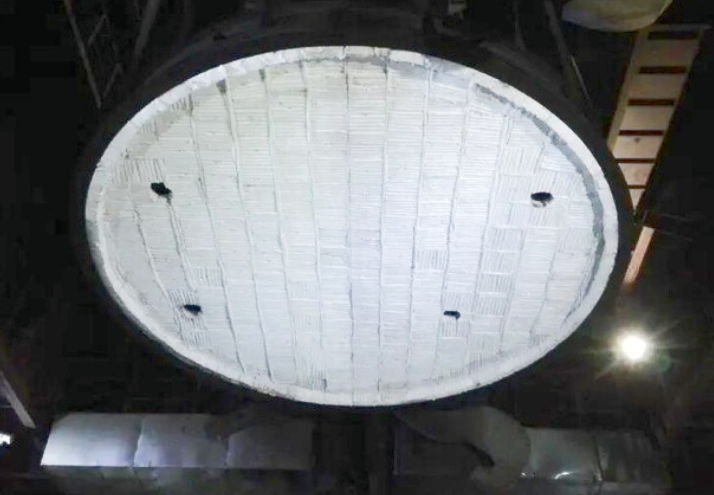
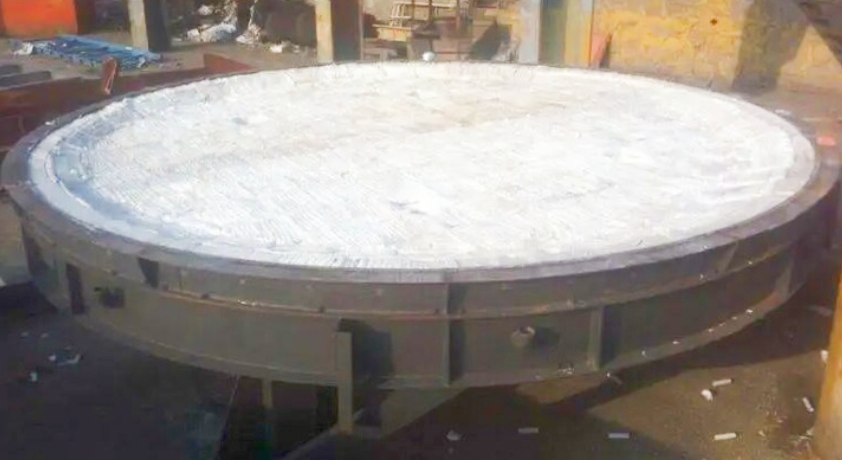
Currently, the vast majority of domestic steel companies use open ladles to hold molten iron. The ladles are placed on iron ladle cars and transported from blast furnaces to steelmaking operation areas using internal combustion locomotives or trucks. In most domestic steel companies, the distance between the blast furnace and the steelmaking operation area is quite far. This segment of the journey is conducted in an open-air environment. This is especially significant during the waiting time for tapping molten iron from the blast furnace and transferring it to the steelmaking area, which can last for 3-5 hours. During the transportation without a cover, and with the ladle being open, the molten iron comes into direct contact with the air. The large temperature difference between the molten iron and the ladle, as well as the air, leads to continuous heat exchange, resulting in a significant amount of heat dissipation. This is particularly pronounced for empty ladles after pouring molten iron, which leads to increased energy consumption, affects the lifespan of the ladle lining, and raises production costs. Additionally, transporting high-temperature molten iron in this manner poses safety risks, which are further exacerbated in adverse weather conditions such as rain or snow.
Excessive temperature reduction of molten iron not only leads to significant temperature drop but also results in wastage of heat, high consumption of iron and steel materials, lack of guarantee for the quality of molten steel, and reduced furnace lifespan. It also affects the oxidation process of elements and the temperature rise rate of the molten pool, which is detrimental to slag formation and impurity removal. Splashing is likely to occur, and in severe cases, tank clogging can disrupt production schedules and affect ladle longevity. Therefore, maintaining stable molten iron temperature upon entering the furnace is of great significance to the converter process.
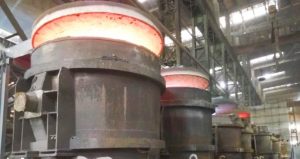
2. Anchor Company's Ceramic Fiber Module Insulation Solution for Molten Iron Ladle Cover
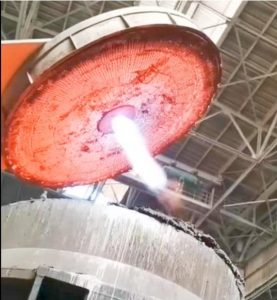
Based on a thorough understanding of the external structure of the molten iron ladle cover, the applied processes, and the surrounding environment, and in consideration of the refractory performance and characteristics of ceramic fiber products, the lining structure of the ladle cover is determined to be a combination of ceramic fiber modules and ceramic fiber blankets. For safety reasons, a ceramic fiber module containing zirconium is generally chosen for the hot surface. The thickness of the insulation layer depends on the operating temperature of the ladle cover, the atmospheric conditions in the environment, and the requirements of the process operations. Ceramic fiber blankets are used as flat linings, typically opting for a lower grade of ceramic fiber blanket with lower zirconium content.
3. Advantages of Anchor Company's Ceramic Fiber Module Insulation
1) Effectively reduces the cooling rate of molten steel and empty ladles, improves the temperature uniformity of molten iron, accelerates the turnover of molten iron ladles, and enhances the quality of steel products.
2) The ceramic fiber module provides excellent thermal insulation performance, reduces heat loss, and has resistance to rapid cooling and heating, as well as resistance to mechanical vibration.
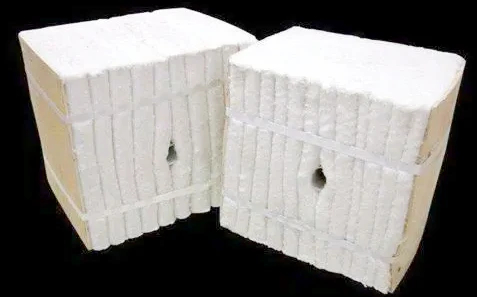
3) Reduces temperature fluctuations in various areas of the molten iron, stabilizes alloy recovery rates, reduces the generation of waste slag inside the ladle, and improves product quality.
4) The ceramic fiber module is a lightweight refractory material, which effectively reduces the load-bearing capacity of the ladle cover’s transmission structure compared to traditional heavy refractory castables.
5) Extends the lifespan of the lifting device; lowers the shell temperature, reduces heat loss, and decreases energy consumption.
6) Improves the working environment for workshop operators.
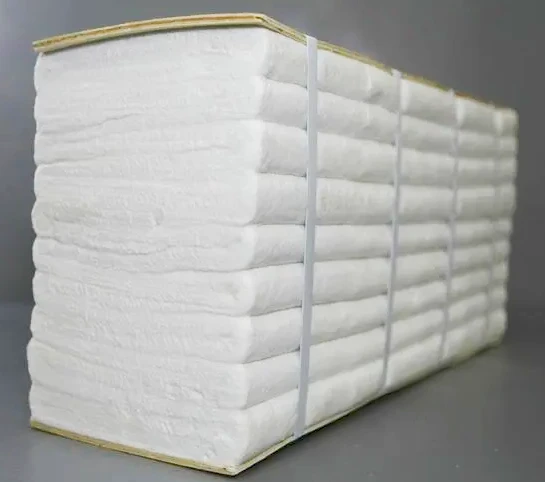