Ceramic Fiber Application in Ethylene Cracking Furnace
Table of Contents
Structural Features of the Ethylene Cracking Furnac
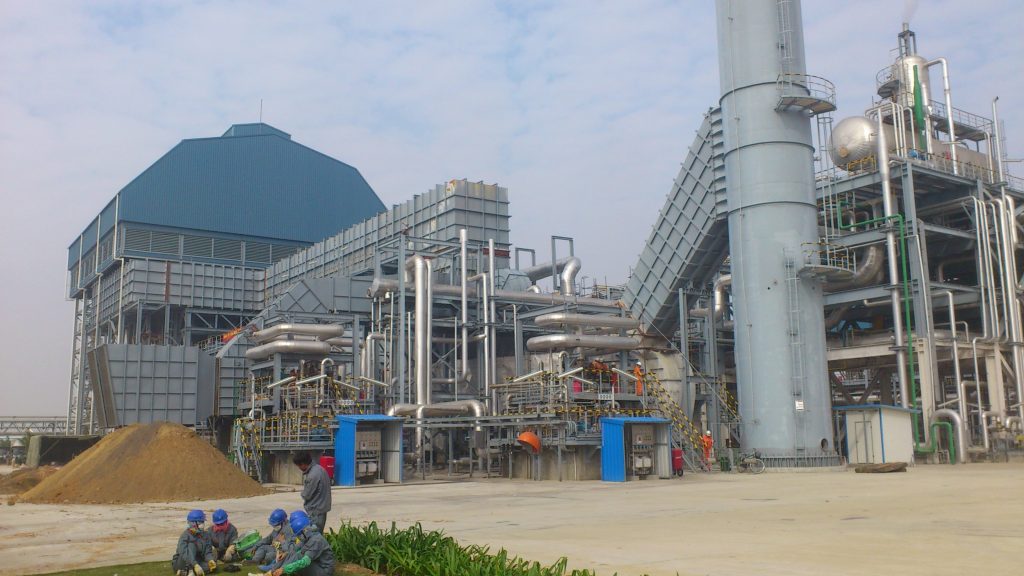
Working Temperature Inside the Furnace and Use of Ceramic Fiber Products
Due to its substantial energy consumption, accounting for 60% of the entire ethylene plant’s energy consumption, enhancing the efficiency of the cracking furnace is crucial to reduce thermal losses. Hence, lightweight zirconia-containing insulation refractory materials from Anchor-Technology are the primary choice for the furnace lining. The working temperature of the furnace tubes is 1100°C, while the radiant section’s temperature generally reaches 1260°C. The refractory lining is a constituent of both the radiant and convection sections of the ethylene cracking furnace. Ceramic fiber modules containing zirconia are commonly chosen for the sidewalls of the radiant chamber, while the refractory lining at the furnace top can be a suspended ceramic fiber structure.
Key Points in the Use of Ceramic Fiber Refractory Lining in the Ethylene Cracking Furnace
Treatment of Burner Nodes on the Furnace Top
After adopting a fully fiber structure for the burners, where fiber materials cannot bear weight, an additional stainless steel fixture is required to secure the burner bricks. Simultaneously, modifications in the external structural shape of the burner bricks are necessary. A critical focus area is the connection between the burner bricks and the ceramic refractory fiber modules. Before installing the modules, envelop the burner bricks with a 20mm zirconia-containing fiber blanket and secure it with heat-resistant wire. After installing the zirconia-containing ceramic fiber modules, compress and seal tightly.
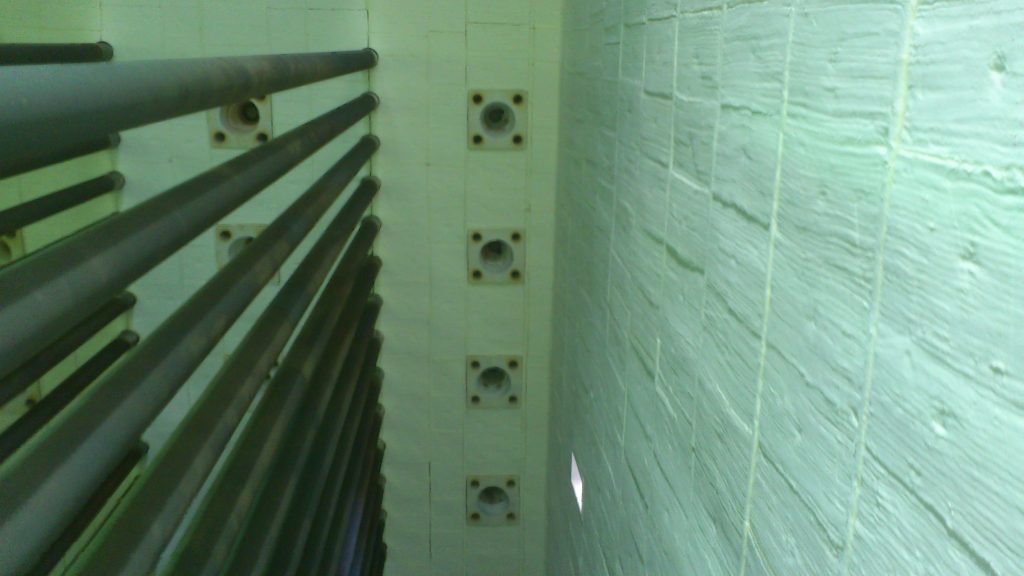
Usage Precautions
In the daily use of the ceramic fiber refractory lining in the cracking furnace, avoid rapid temperature changes when starting or stopping the furnace. Adjust the expansion joints promptly to meet requirements, preventing cracking or detachment of the ceramic fibers in the convection section. In the event of incidents of cracking or detachment, promptly replace the ceramic fiber lining and readjust the expansion joint positions.
Maintenance Precautions
In the daily use of the ceramic fiber refractory lining in the cracking furnace, avoid rapid temperature changes when starting or stopping the furnace. Adjust the expansion joints promptly to meet requirements, preventing cracking or detachment of the ceramic fibers in the convection section. In the event of incidents of cracking or detachment, promptly replace the ceramic fiber lining and readjust the expansion joint positions.
Fiber Module Treatment
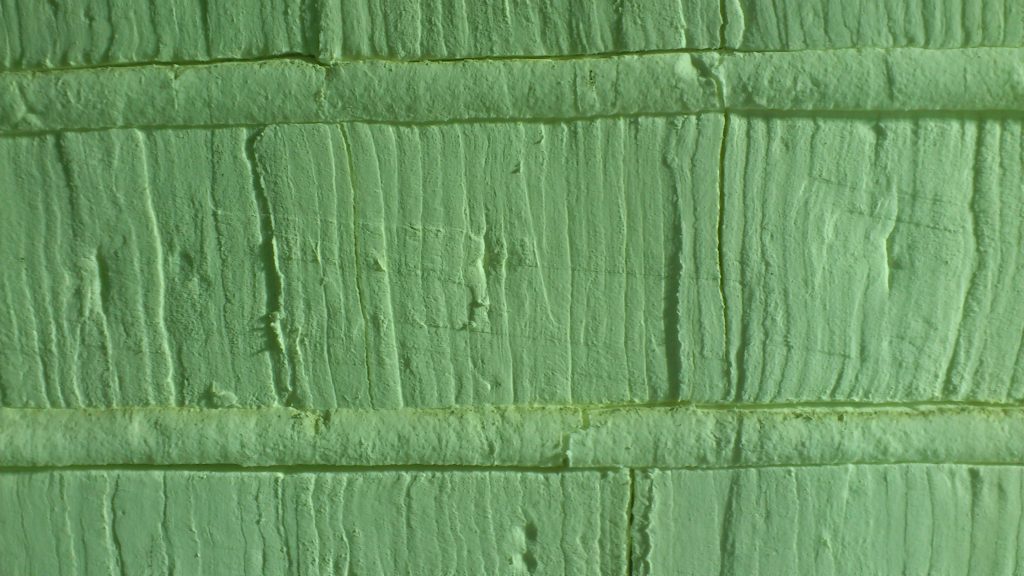