The Energy-saving Effect of Ceramic Fiber Chromium Modules in Forging Furnaces
Table of Contents
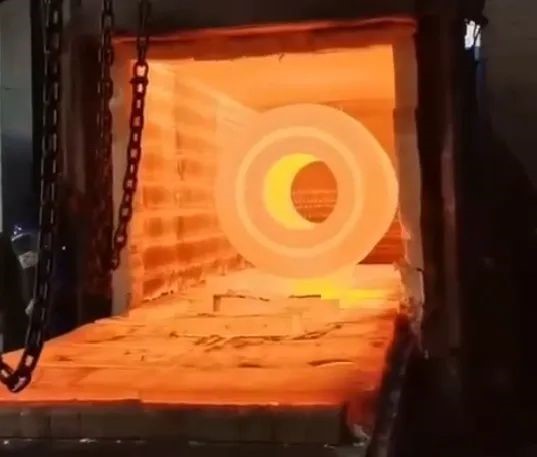
Anchor-Technology’s ceramic Fiber chromium modules, with a classification temperature of 1500℃, are excellent insulation materials for furnace linings with high-temperature requirements. The energy-saving effect of ceramic fiber modules has been widely recognized by customers in the heat treatment equipment industry in recent years, exhibiting a significantly higher usage rate compared to other insulation refractory materials. In this article, Anchor-Technology will walk you through the outstanding energy-saving effect of ceramic Fiber chromium modules in forging furnaces!
Benefits of Using Anchor-Technology Ceramic Fiber Chromium Modules:
- Energy-saving: For heat treatment equipment such as pit furnaces, car bottom furnaces, and forging furnaces, Anchor-Technology’s ceramic Fiber chromium modules exhibit outstanding energy-saving effects, mainly due to their ultra-low thermal conductivity and excellent insulation properties.
- Rapid Heating: The far-infrared radiation effect generated during the heating process by components such as SiO2 and Cr₂O₃ in the product helps in rapid heating.
- High Equipment Utilization: The light-reflective effect produced by the low heat capacity of ceramic Fiber reduces heat loss. Simultaneously, by shortening the heating time and retaining furnace heat, it significantly improves equipment utilization.
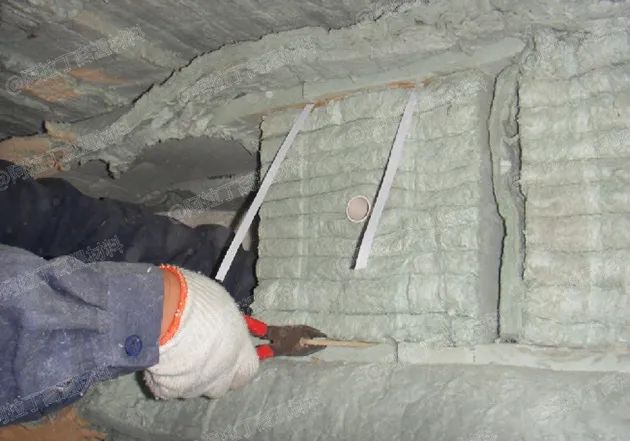
Easy to install:
Anchor-Technology’s ceramic Fiber chromium modules are easy to install, quickly adaptable, and do not require furnace drying. This saves bricklaying costs and shortens commissioning time.
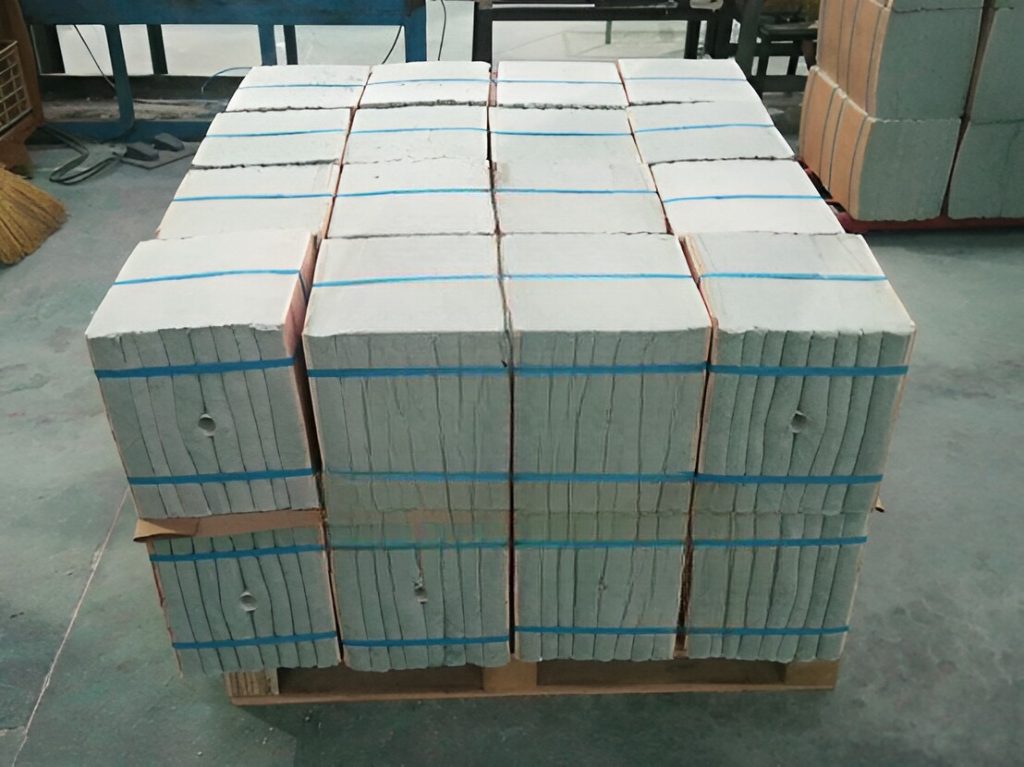
Low cost:
Compared to other refractory materials, Anchor-Technology’s ceramic fiber modules are relatively low in cost but offer high efficiency. If smoothly operated, the costs can be recovered within a month. Moreover, under conditions without external forces, wind speed, or friction, they have a longer service life, averaging 5 years. However, due to their low mechanical strength, they are susceptible to wear and tear, especially in high-speed furnace atmospheres, leading to potential peeling. Therefore, it’s advisable to periodically apply Anchor-Technology’s high-temperature protective coatings or check the lining to replace old modules.