Carbon Baking Furnace Ceramic Fiber Insulation Scheme
Table of Contents
Overview of Carbon Baking Furnace
Introduction to the Carbon Baking Furnace
The carbon baking furnace is a type of thermal equipment used for the indirect heating of various carbon products formed under high pressure conditions. This process occurs at specified baking temperatures in an oxygen-deprived environment, enhancing the conductivity and thermal properties of the products, thereby improving their strength.
Insulation Structure of Carbon Baking Furnace
The insulation of the carbon baking furnace is classified into the furnace bottom, side walls, combustion walls, transverse walls, furnace top, and flue.
Types of Carbon Baking Furnace
There are two types of carbon baking furnaces: open circular and covered circular types. These are primarily utilized for the baking of carbon anodes for aluminum and for baking steel electrodes. Currently, open circular baking furnaces are used for aluminum carbon anode baking.
The production practice demonstrates that the heat utilization and heat loss of the baking furnace account for approximately fifty percent each. Therefore, reducing fuel consumption in the baking process of aluminum carbon anodes has long been a significant issue in the carbon industry.
Production Challenges of the Carbon Baking Furnace
Serious negative pressure leakage, unstable operation, substantial heat loss, and decreased product qualification rates are escalating costs for enterprises. Negative pressure leakage mainly occurs due to poor quality, deformability, and easy cracking of furnace wall materials, causing difficulties in creating negative pressure.
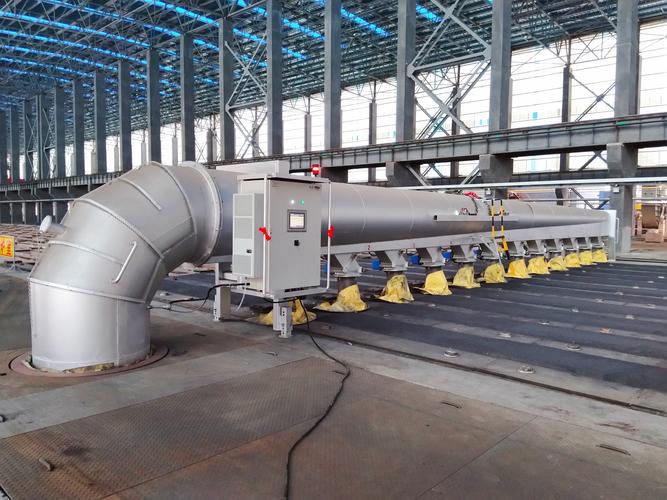
Ceramic Fiber Insulation Scheme
(1) Impregnation System Insulation
Insulation Structure of the Impregnation Heating Furnace
The impregnation heating furnace, also known as the preheating furnace, operates at temperatures not exceeding 650°C, with the combustion chamber operating at 800°C using gas heating.
It employs a composite structure of 1050-type ceramic fiber blankets and 1050-type ceramic fiber modules. The furnace walls, walls, and doors have an insulation thickness of 280mm, consisting of a 30mm 1050-type ceramic fiber backing blanket and a 250mm 1050-type ceramic fiber module. The furnace top has an insulation thickness of 350mm, with a structure of a 50mm 1050-type ceramic fiber backing blanket and a 300mm 1050-type ceramic fiber module.
Insulation Structure of the Combustion Chamber at the Top of the Heating Furnace
The insulation thickness is 350mm, comprising a 50mm 1050-type ceramic fiber backing blanket and a 300mm 1050-type ceramic fiber module.
External Insulation Structure of the Impregnation Tank
The working temperature of the impregnation tank is 300°C. To prevent worker burns, heat loss, and corrosion, external insulation is required.
The insulation layer consists of a 100mm thick 1050-type ceramic fiber blanket and a 0.5mm thick colored steel plate. Given the varying tank sizes and numbers, a professional construction team is recommended to install steel frames as required.
(2) Baking System: Design of Circular Baking Furnace Insulation Structure
Working Temperature of the Furnace Lining
The long-term working temperature is 1250°C, using gas heating.
Furnace Lining Material
It adopts a composite structure of zirconium-containing ceramic fiber modules and zirconium-containing ceramic fiber blankets. The insulation thickness is 350mm, comprising a 50mm zirconium-containing ceramic fiber backing blanket and a 300mm zirconium-containing ceramic fiber module.
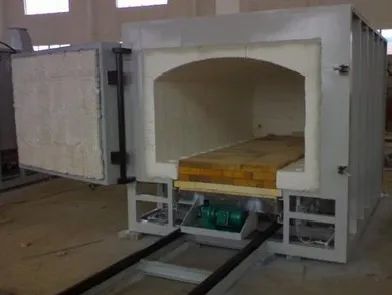