Main Structure of All-Ceramic Fiber Lining in Heating Furnaces
Table of Contents
In the structure of the furnace lining, the all-ceramic fiber lining structure is roughly divided into four forms. Each form has its own advantages and disadvantages in the application process. Therefore, when choosing, it is necessary to select based on different practical needs to maximize the effectiveness of the all-ceramic fiber lining.
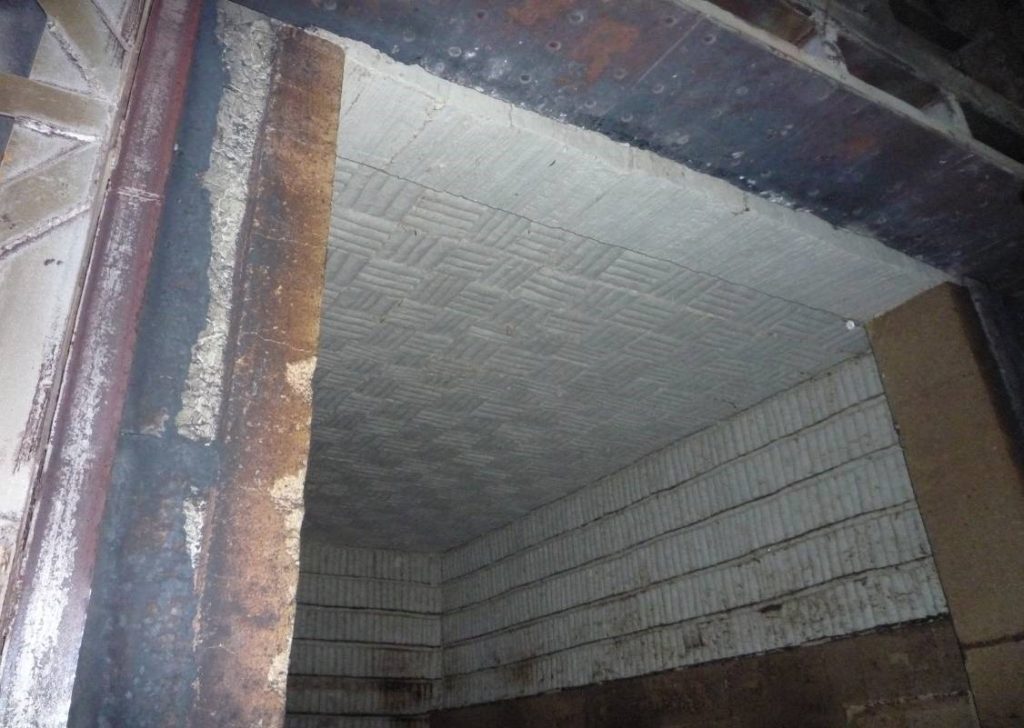
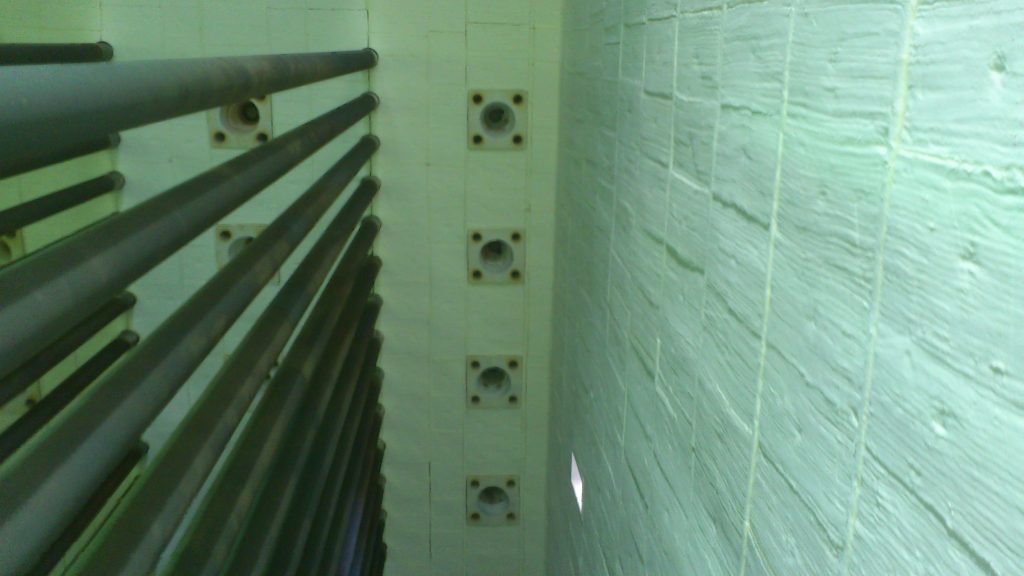
I. Single-Layer Spread-Type All-Ceramic Fiber Lining Structure
(1) Introduction to Single-Layer Spread-Type Lining Structure:
The single-layer spread-type lining structure primarily refers to a mechanically fixed structure. Anchors are used to fix the lining during the fixing process. Bolts, anchor washers, and nuts are typically used for fixation, along with ceramic fasteners such as combinations of magnetic pins and caps, which are commonly used during lining fixation.
The main purpose of lining fixation is to effectively secure the all-ceramic fiber lining and other related insulation materials to the steel plate of the heating furnace’s shell in a spread-out manner.
(2) Characteristics of Single-Layer Spread-Type Lining Structure:
- Single-layer spread-type lining can select appropriate fixing materials based on different heating temperatures of each part.
- It exhibits a lower thermal conductivity during fixed application, allowing the lining to store heat automatically, effectively preventing heat loss.
- This type of lining construction is faster in the installation process and offers greater flexibility.
- During the single-layer spread construction process, it’s essential to use fasteners for lining fixation. Exposed fasteners in the furnace must not experience excessively high temperatures during furnace operation to prevent their melting and affecting the performance of the all-ceramic fiber lining.
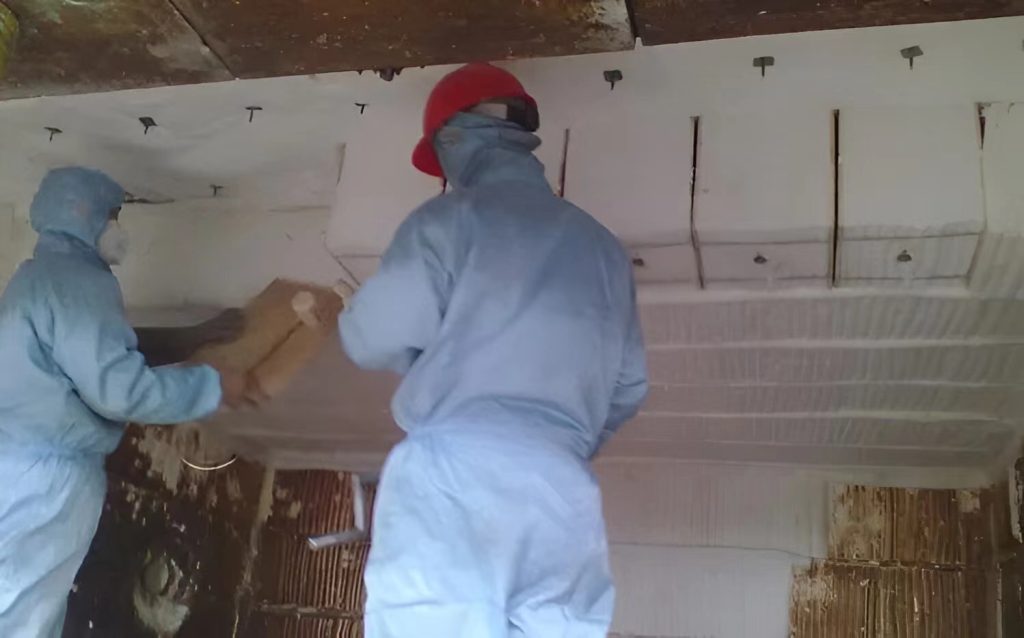
II. Double-Layer Overlap-Type All-Ceramic Fiber Lining Structure
(1) Introduction to Double-Layer Overlap-Type Lining Structure:
The double-layer overlap-type all-ceramic fiber lining primarily consists of three parts: stacked plates, prefabricated modules in folded blanket form, and prefabricated blocks in overlaid felt form. During construction, bonding and mechanical fixation are the main methods. The lining can be overlapped in a “brick-laying” manner.
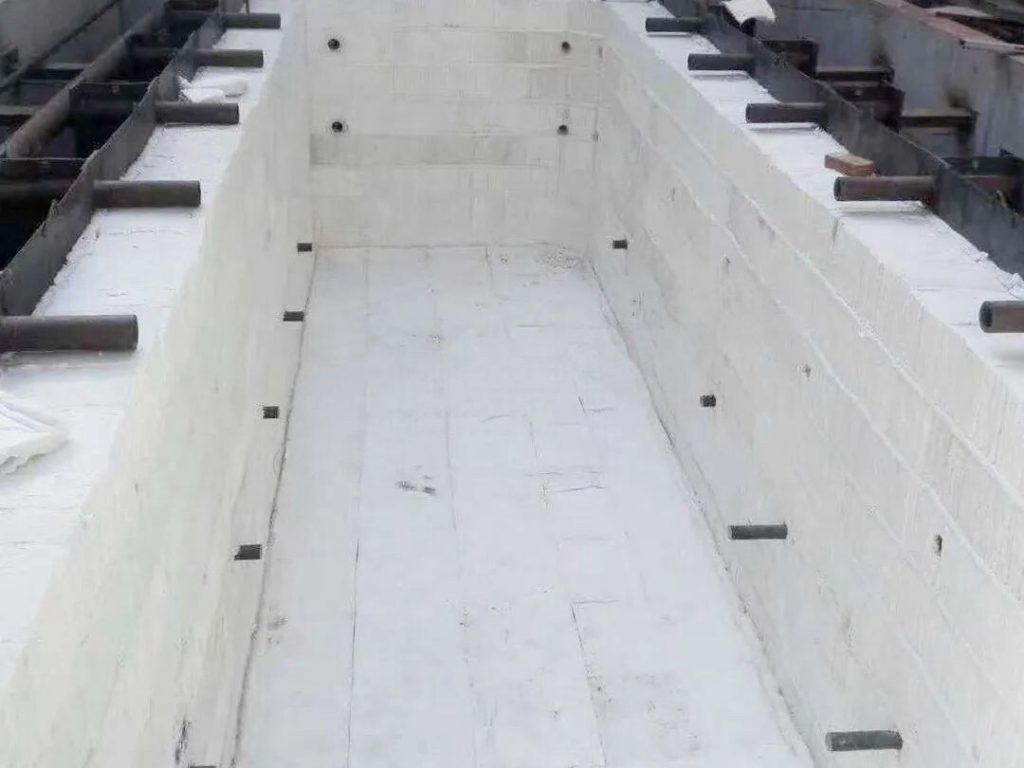
(2) Characteristics of Double-Layer Overlap-Type Lining Structure:
- Compared to single-layer spread linings, double-layer overlap linings exhibit better heat resistance, allowing for a temperature increase of over 50°C within the furnace chamber.
- It displays relatively better resistance to erosion from wind.
- There’s no use of fasteners during the fixing process, effectively reducing construction costs and allowing for cost control.
- With higher thermal conductivity, the furnace’s thickness must increase by at least 1/4 during the installation of this lining form to prevent excessive furnace temperatures.
III. Prefabricated Blanket-Type All-Ceramic Fiber Lining Structure
(1) Introduction to Prefabricated Blanket-Type Lining Structure:
The main structure of the prefabricated blanket-type all-ceramic fiber lining is in a steel framework form. A certain thickness of steel plate or steel mesh is welded to the upper part of the steel framework, and heat-resistant fasteners are also welded during this process. After welding, ceramic fiber blankets with good insulation properties are effectively fixed on the steel framework through the action of adhesives, forming different furnace wall panels based on varying specifications.
(2) Characteristics of Prefabricated Blanket-Type Lining Structure:
- It exhibits a higher degree of standardization in design and construction, offering strong interchangeability.
- It simplifies the construction process, effectively shortening the construction period.
- It is cost-effective, significantly reducing production and operational costs.
- The design and production of the prefabricated blanket-type lining require excellent control over its airtightness. If sealing issues arise, it can significantly affect the lining’s functionality.
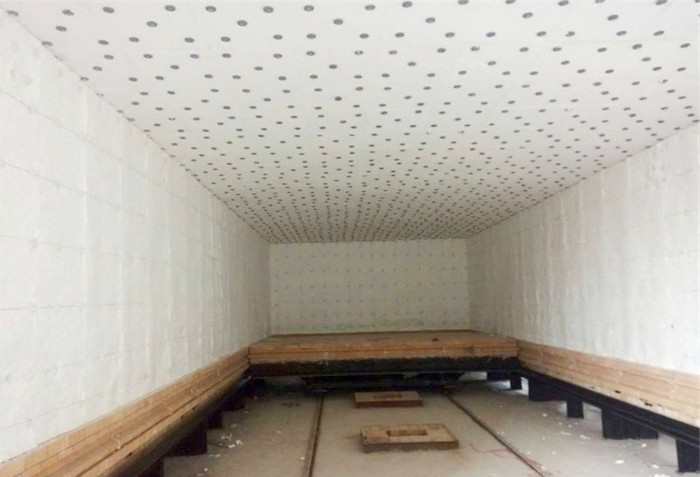
IV. Vacuum Molded Shell-Type All-Ceramic Fiber Lining Structure
(1) Introduction to Vacuum Molded Shell-Type Lining Structure:
The vacuum-molded furnace structure primarily uses vacuum molding technology for the lining’s production. During fabrication, the fiber lining is shaped into a shell with approximately 15mm thickness, having five faces. A certain amount of all-ceramic fiber is added inside the shell, and ceramic fiber cotton is tied to the outer surface of the shell, fixed by fasteners.
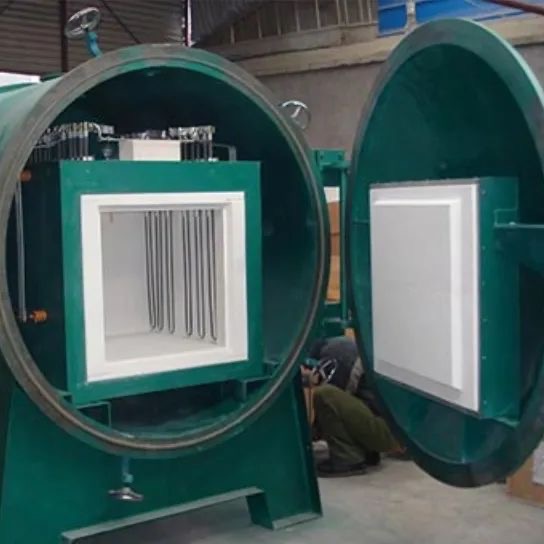
(2) Characteristics of Vacuum Molded Shell-Type Lining Structure:
- It’s relatively easy to construct in a masonry process, and the utilization of construction materials is exceptionally high, saving materials.
- It is suitable for linings with special requirements, meeting specific demands.
- The vacuum molded lining demands higher requirements in production and manufacturing processes, thus significantly increasing production costs.
V. Selection and Application Considerations:
In the choice of furnace lining structures, several considerations are essential:
Temperature Variation: Different furnace linings may respond differently to varying temperatures within the furnace. It’s crucial to select a lining structure that suits the temperature requirements of different furnace zones.
Heat Loss Prevention: The capacity of the lining to retain heat and prevent heat loss varies across different structures. Opt for a lining that efficiently conserves heat to enhance furnace performance.
Construction Speed and Flexibility: Construction speed and flexibility differ among the various lining structures. Choose a structure that aligns with construction timelines and offers flexibility where required.
Cost Efficiency: The cost-effectiveness of different lining structures is a significant factor. Consider not only the initial construction costs but also long-term operational expenses and maintenance requirements.
Material Compatibility: Assess the compatibility of the chosen lining structure with the materials used in the furnace’s operations to avoid adverse reactions or performance issues.
Sealing and Durability: Ensure the selected lining structure provides adequate sealing and durability to withstand the operational conditions within the furnace over its intended lifespan.
By considering these factors, the most suitable all-ceramic fiber furnace lining structure can be selected, optimizing its functionality and ensuring efficient furnace operation.