Ceramic Fiber Insulation Scheme for Methanol Conversion Furnace
Table of Contents
I. Overview of Methanol Conversion Furnace
The insulation considerations for a methanol conversion furnace include furnace type, temperature, heating methods, and furnace atmosphere. Furnace types mainly include top-burning box-type, side-burning dual-chamber type, small cylindrical type, etc. The furnace typically utilizes natural gas with added vapor, maintaining a relatively clean combustion with a sulfur content not exceeding 50ppm. The radiation section operates under a slight negative pressure (-5~-10mmH2O), with a maximum designed temperature of 1260℃. The furnace interior maintains a weak reducing gas atmosphere.
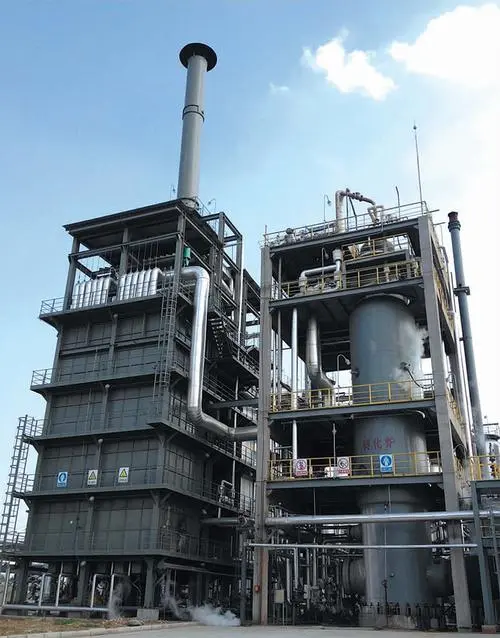
II. Ceramic Fiber Insulation Scheme for Methanol Conversion Furnace
ethanol Conversion Furnace – Convection Section Ends and Sides Insulation Lining Thickness: 180-200 mm Lining Structure: 160mm 1260℃ high-purity ceramic fiber modules + 20-40mm backing of 1260℃ standard ceramic fiber blankets Anchoring Material: S304 stainless steel
Methanol Conversion Furnace – Convection Section Upper Insulation External Insulation Thickness: 30mm Lining Structure: 30mm 800℃ soluble-type ceramic fiber blanket
Methanol Conversion Furnace – Convection Section Bottom Insulation Lining Thickness: 180-200 mm Lining Structure: 160mm 1260℃ high-purity ceramic fiber modules + 20-40mm backing of 1260℃ standard ceramic fiber blankets
Requirements for External Wall Temperature of Methanol Conversion Furnace:
Under design conditions with a wind speed of 2.0 meters/second and an ambient temperature of 25℃, except for the furnace door and joint areas, the external wall temperature of the furnace should not exceed the specified temperature. The average external wall temperature of the furnace body: ≤80℃.
III. Advantages of Ceramic Fiber Lining in Methanol Conversion Furnace
- Difficulty in lining construction arises due to the expansion and movement of the furnace pipes after heating, improper handling may lead to flashovers, resulting in heat loss, oxidation, and deformation of the suspended pipe rack. A well-designed ceramic fiber module structure can reduce construction difficulties and create an effective seal between the alumina-silicate furnace lining and the furnace pipes.
- The ceramic fiber modules are compressed against the furnace pipes. Due to the elastic rebound after compression, the ceramic fibers can absorb and compensate for the gaps caused by the volume changes in the furnace pipes due to thermal expansion and contraction.