How to Maintain the Refractory Fiber Lining of a Mesh Belt Kiln
Table of Contents
Overview of the Mesh Belt Kiln
- The mesh belt kiln belongs to a continuous type furnace, utilizing a metal mesh belt as the driving mechanism, supported by rollers or plates. It is primarily employed in ceramic glass firing, glass heat bending, glass annealing, catalysts, and the drying and firing of powdered materials. Mesh belt kilns can be classified into flame-heated and electric-heated types. The choice of stainless steel material for the mesh belt depends on the temperature requirement, typically operating at <1000℃, accommodating various atmospheres.
- The furnace lining of a mesh belt kiln generally uses Anchor-Tech ceramic fiber products, which have a low thermal conductivity and excellent insulation. This choice reduces the wall thickness of the furnace, decreases the furnace volume, and saves transportation costs. For mesh belt kilns that demand high cleanliness inside, ceramic fiber boards are commonly used as furnace linings. However, even after prolonged use, ceramic fiber boards might exhibit powder shedding due to the inherently porous nature of refractory fibers.
- Ceramic fiber boards are composed of ceramic fiber material, mainly used as a refractory insulation material in steel ladle linings, industrial furnace linings, high-temperature equipment, and other non-direct fire surfaces. These boards are often combined with refractory bricks or heavy-duty castables to provide thermal insulation. They are also used in the hot surfaces of muffle furnaces, mesh belt furnaces, and other industrial furnaces.
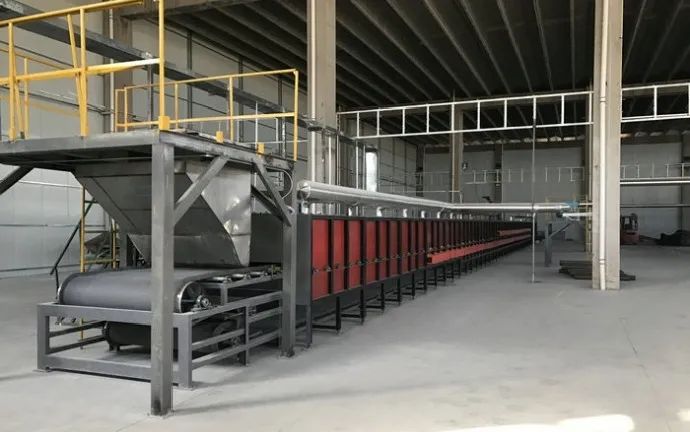
Anchor-Tech ceramic fiber boards have a density ranging from 300-350Kg/m3. These boards are made from high-purity ceramic fiber cotton, processed through pulping, mineral filler addition, inorganic binders, organic additives, and manufacturing processes like sheet forming, vacuum filtration, shaping, drying, etc. They find primary application in high-temperature insulation fields. Anchor-Tech’s advanced production technology ensures uniform fiber distribution, strict control over board thickness, and volume density with minimal error.
The solution to the shedding issue of refractory fiber linings in a mesh belt kiln
Ceramic Fiber Anti-Slagging Coating Effectively Addresses Surface Powder Shedding Issues of Ceramic Fiber Boards.The ceramic fiber anti-slagging coating is a water-based, non-combustible coating with an A-grade fire rating. It exhibits strong adhesion and thermal shock stability on the surface of ceramic fibers, preventing cracking and flaking even under extreme temperature fluctuations. The coating offers excellent resistance against dust abrasion, maintaining a robust bond and thermal stability with ceramic fibers at high temperatures.
The environmentally friendly and non-toxic coating forms a dense protective layer on the surface, providing strong resistance against rust, corrosion, discoloration, acid, alkali, and aging. It is easy to apply, operate, and extends the service life of the base material. This product is non-toxic and exhibits good stability during storage and application. In acid salt spray and high-temperature and high-humidity tests, its corrosion resistance is improved by over 3 times. Its metal anti-discoloration ability is 20 times better than chromium acid passivation. Furthermore, it shows outstanding resistance to aging in high-temperature sulfur dioxide and hydrogen sulfide gas corrosion tests. The coating displays excellent adhesion, high hardness, and wear resistance.