Energy-saving Application of Ceramic Fiber Modules in the Iron and Steel Industry
Table of Contents
Overview of the Application of Ceramic Fiber Modules in Steel Furnaces
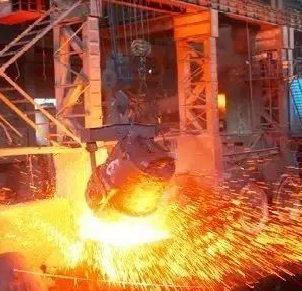
In the heating furnace applications of the iron and steel industry, ceramic fiber modules are primarily used for steel ladle covers, steel billet transfer cars, and furnace walls in heat treatment furnaces. Currently, ceramic fiber modules are extensively used as linings in heat treatment furnaces with high cleanliness requirements.
Specific Applications of Ceramic Fiber Modules in Steel Furnaces
- In the annealing furnace for cold-rolled strip steel, ceramic fiber modules are used as linings from the heating section to the cooling section, covering from the furnace top to the furnace bottom.
- In the direct-fired heating section of the preheating stage, hollow modules are used to facilitate the direct installation of burners.
- For the furnace walls in the heating section, ceramic fiber modules are installed to accommodate the installation of radiant tubes.
- At the neck of furnace rollers, modules can be shaped like trumpet mouths, making it easy to install the furnace lining.
- To prevent fiber shedding and contamination of the strip steel, aluminum foil can be sewn onto the modules as a lining.
- In special-shaped areas such as furnace throat and furnace bottom, Anchor-Tech ceramic fiber shaped modules can be used.
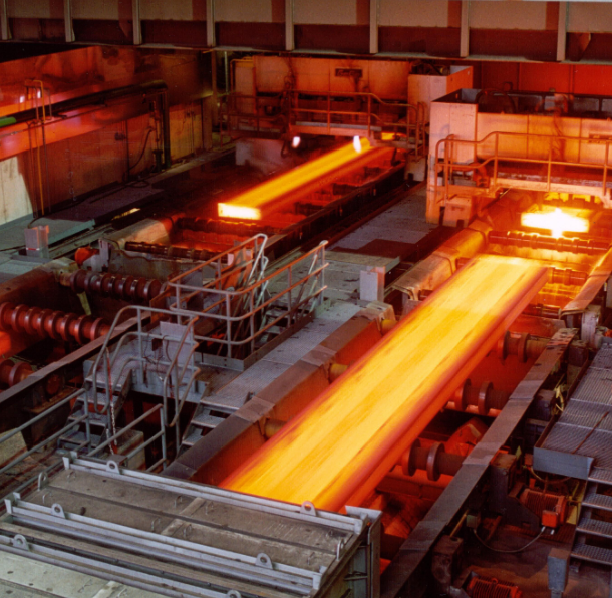
Summary of Energy-saving Effects
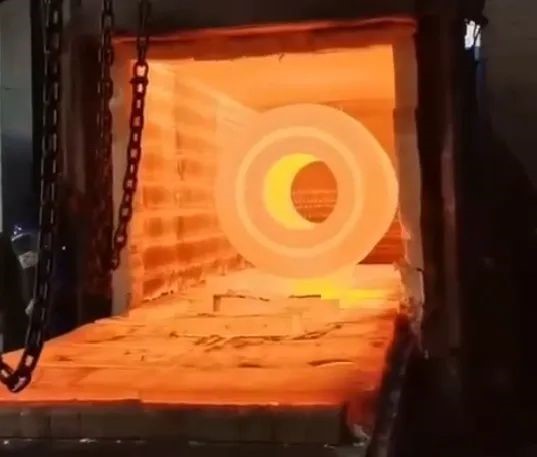
- The furnace temperature of steel heat treatment furnaces is typically below 1300°C, with medium-temperature furnaces slightly lower (650~1000°C), and low-temperature furnaces below 650°C. Anchor-Tech ceramic fiber modules play a crucial role in reducing heat storage and heat dissipation losses, contributing significantly to improving furnace thermal efficiency and saving energy.
- Previously, lightweight refractory bricks with a bulk density of 1.3 were commonly used as furnace linings in heat treatment furnaces. However, the high self-weight of the lining imposed a significant load on the furnace structure, leading to serious heat dissipation losses due to high thermal conductivity.
- Taking a 300KW electric hood furnace as an example, when the refractory lining is changed to a full-fiber composite structure using ceramic fiber modules and blankets, the lower bulk density and specific heat of ceramic fiber compared to clay bricks effectively reduce heat storage and heat dissipation losses. This results in an energy savings of 38.3% compared to a lightweight clay brick structure.
Anchor-Tech Ceramic Fiber Modules
Anchor-Tech ceramic fiber modules/blankets are alumino-silicate refractory materials with a high refractory temperature (1000-1500°C), stable chemical properties, low thermal conductivity, low bulk density, and long service life. They are essential furnace lining materials for steel heat treatment furnaces.