Table of Contents
Anchor-Tech takes you through ceramic fiber modules
Ceramic fiber modules, as low thermal conductivity, lightweight and energy-saving refractory materials, are widely used in many heat treatment furnaces (rolling furnaces, annealing furnaces, trolley furnaces, pit furnaces, etc.). At present, the use of ceramic fiber furnace lining has become institutionalized and normalized, and the materials must be used in furnace overhaul.
So do you know these little things about ceramic fiber modules? Anchor-Tech will tell you some useful tips today!
1. Energy-saving effect of ceramic fiber modules
Studies have shown that the proper use of ceramic fiber in industrial furnaces can greatly reduce fuel consumption. Gas furnaces can reduce gas consumption by about 35%, oil furnaces can reduce fuel consumption by 26%, and electric furnaces can reduce electricity consumption by 48%.
Not only that, the use of ceramic fiber furnace lining can also effectively extend the service life of the furnace body. Lightweight ceramic fiber refractory material can greatly reduce the amount of steel used in the furnace body. In some cases, it can replace refractory bricks and reduce the weight load of the furnace body, thereby extending the service life of the furnace body.
2. What characteristics does a good ceramic fiber module need to have?
① It has good high temperature resistance, does not soften or collapse under continuous high temperature, and the 24-hour linear shrinkage is less than 3%.
② Good thermal shock resistance, resistance to rapid cooling and rapid heating, and will not cause furnace lining cracking due to excessive temperature difference between starting and stopping the furnace.
③Good chemical stability, not easily corroded by acid, alkali and corrosive atmosphere, long service life.
④ Lower thermal conductivity and smaller heat capacity improve the thermal sensitivity of the furnace, reduce heat loss, and improve product quality.
⑤Simple structure, convenient construction, no need for oven, easy maintenance and repair.
3. Low heat storage of ceramic fiber modules
Generally speaking, materials with higher density have greater heat storage, that is, greater thermal inertia, which is reflected in the slow heating and cooling of the furnace and serious heat storage losses. Ceramic fiber modules are lightweight refractory materials with a density of 220kg/m3, which is about 1/4 of heavy refractory bricks. The lower density enables ceramic fibers to have a small heat capacity per unit volume or unit thermal resistance.
Experiments have shown that different furnace insulation materials have a great impact on the furnace heating time.
Taking the intermittent heating furnace as an example, when the furnace temperature rises from 1200 degrees to 1270 degrees, the ceramic fiber module furnace body takes 10 minutes, while the heavy refractory bricks take 70 minutes. In other words, under the same heating conditions, the heating time of the ceramic fiber furnace body is 1 hour shorter than that of the refractory converter body, which is equivalent to saving 1 hour of fuel . The significance of this for manufacturers to save energy and reduce costs is self-evident.
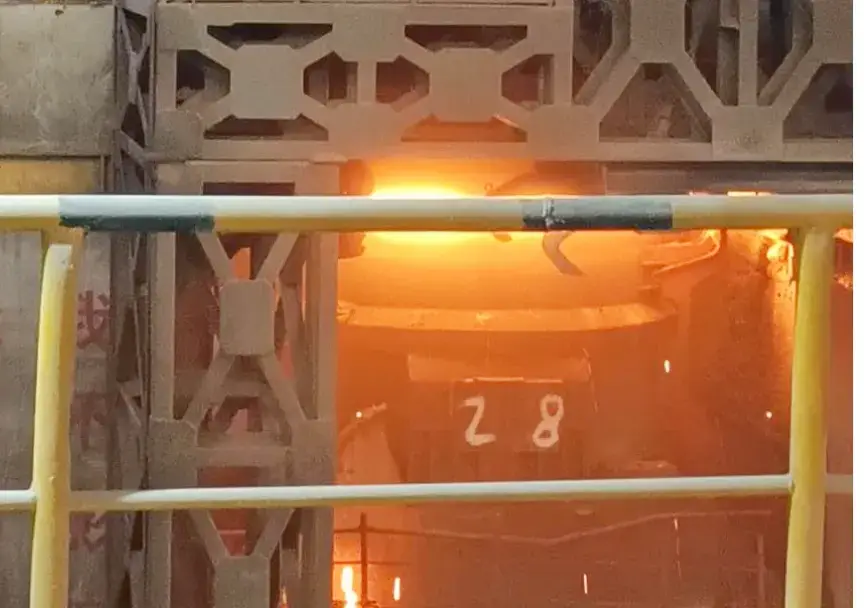
4. How to extend the service life of ceramic fiber modules
① The premise is that the design of the insulation plan must be standardized, the selected refractory materials have the correct operating temperature, and there will be no collision between machinery and workpieces.
② Select the appropriate grade of product based on the use environment, temperature, atmosphere, and wind speed, including classification temperature, density, surface treatment, specifications, etc.
Reasonable material selection is the basis for ensuring the service life of the product.
③The installation process and construction quality are important factors in ensuring the service life of the refractory fiber furnace lining. Refractory fibers such as ceramic fiber modules generally have a pre-compression amount during installation to compensate for the linear shrinkage of the fibers when heated. During installation, construction must be carried out in strict accordance with the drawings to ensure the firmness and sealing of the furnace lining.
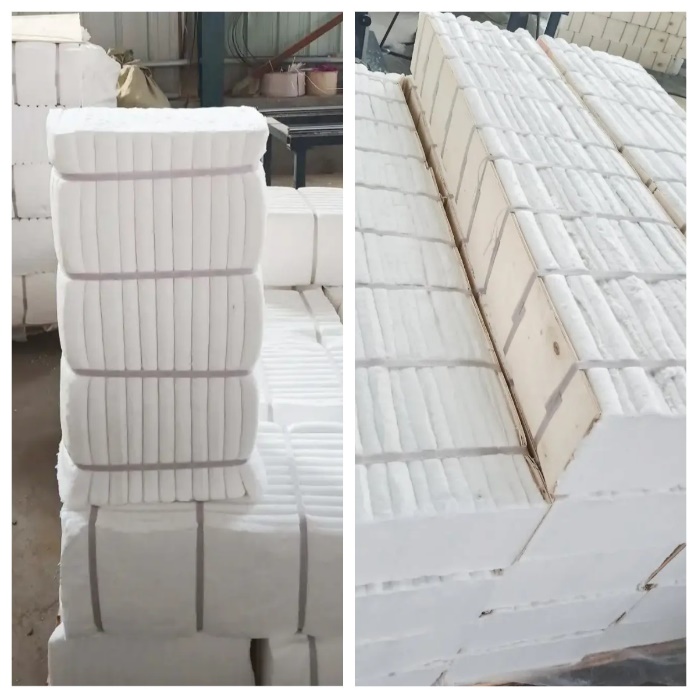