Table of Contents
Ceramic fiber high temperature solution for walking beam heating furnace
1. Introduction to furnace structure and function
Walking beam furnace is a continuous furnace. The temperature section in the furnace is divided into preheating, heating (high temperature), and soaking (insulation) sections. The walking beam is a water-cooled beam (a few are heat medium cooling beams for vaporization cooling and high-pressure water high-temperature cooling) or a heat-resistant steel beam. It is mostly used for quenching, pre-normalizing heating, and tempering heat treatment heating in the heat treatment of long workpieces. The furnace temperature is 900-1300℃, and the fuel is gas and heavy oil .
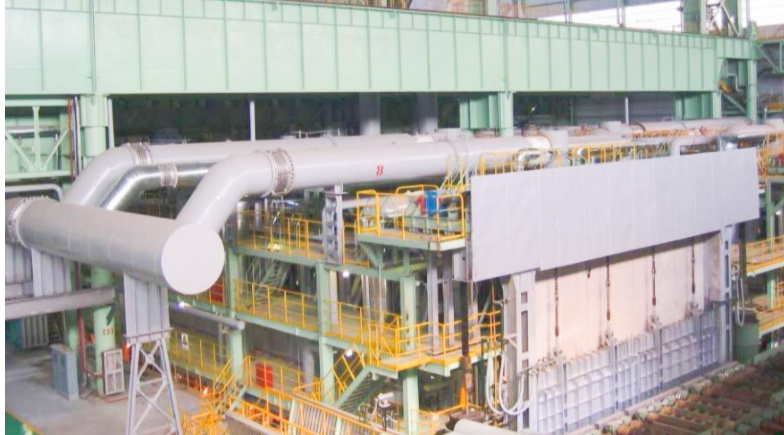
2. Introduction to wall lining materials and insulation thickness
A. Wall lining material : According to the process operating temperature and operating characteristics of each working section of the walking beam furnace, aluminum silicate fiber wall lining ( referring to the full fiber structure) is only suitable for the preheating section. In addition, ceramic fiber blankets , ceramic fiber boards and other products can be combined with refractory castables, lightweight bricks and other products to form composite linings for soaking sections, heating sections and water beam wrapping. For walking beam furnaces using heat-resistant steel beams, the furnace temperature generally does not exceed 1050°C due to the material of the beams ). Low-zirconium and zirconium-containing ceramic fiber modules and ceramic fiber blankets can be used to stack furnace linings for the furnace walls and roofs .
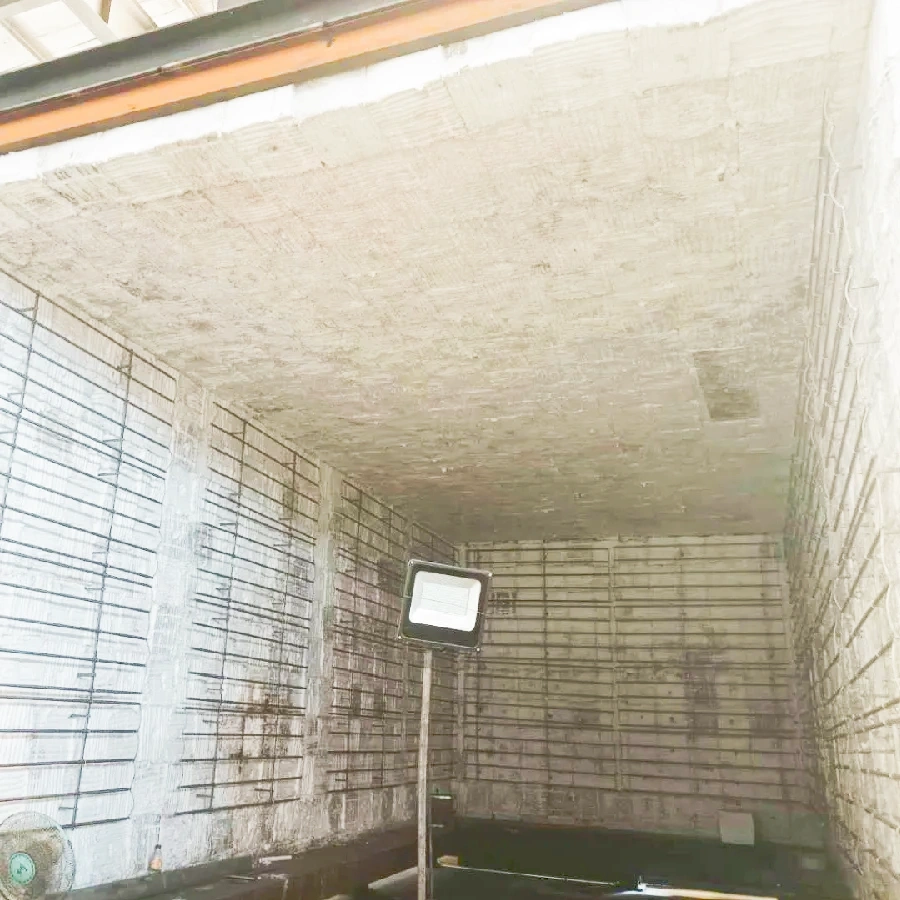
B. Determination of insulation thickness: Using ceramic fiber wall lining with a thickness between 250-350mm can achieve better insulation and energy-saving effects.
3. Recommended wall lining structure
a preheating section that can adopt a full fiber structure, a composite lining of flat ceramic fiber blanket and stacked ceramic fiber modules is often used. The flat backing adopts ceramic fiber needle blanket . During construction, heat-resistant stainless steel anchors are welded and fast cards are pressed in to fix. 2~3 layers are laid flat , and the thickness is generally 50~80mm . The stacked working layer adopts ceramic fiber modules and prefabricated components (including hanging, sliding , and angle iron structures) folded and compressed by ceramic fiber needle blanket . The thickness of the fiber component is generally 200-270mm .
In addition, composite fiber spray lining can also be used for the preheating section wall lining . The backing spray fiber can be ordinary or standard, and the working hot surface layer uses high aluminum or zirconium aluminum fiber, with thicknesses of 50~80mm and 160~200mm respectively , and pre-buried heat-resistant insulation nails and quick cards and heat-resistant steel wires are pressed layer by layer according to the construction layer to fix the lining.
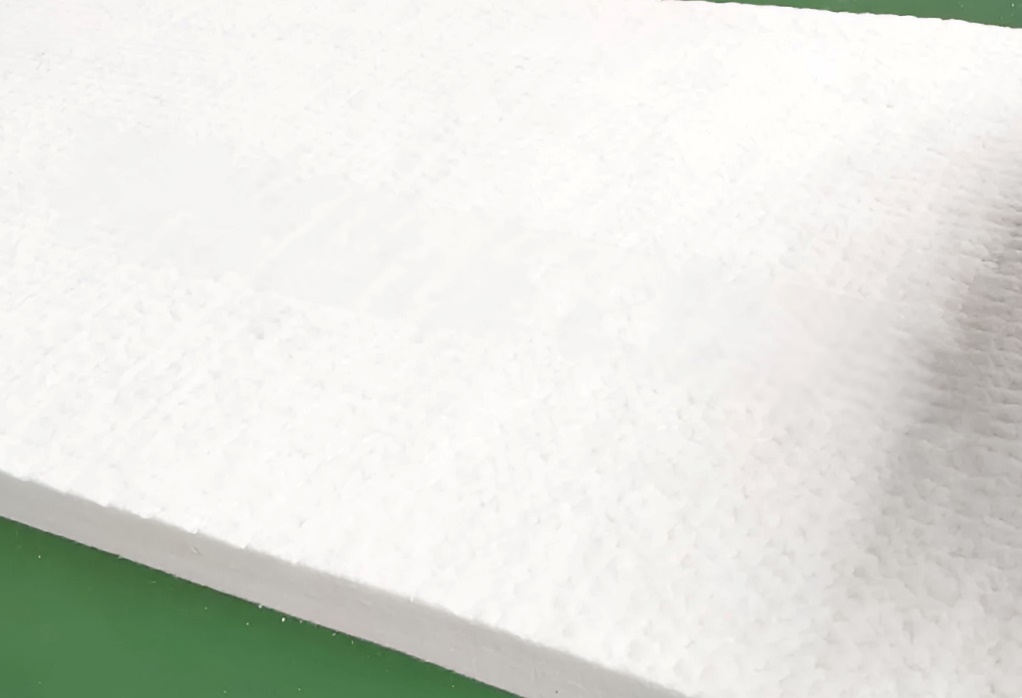
4. Ceramic fiber wall lining installation arrangement structure
The ceramic fiber blanket backing is to spread the rolled ceramic fiber blanket , straighten it, press it flat on the furnace wall steel plate, and press it into the quick card to fix it. The staggered distance between layers is required to be greater than 100mm to avoid straight seams.
blankets are added between rows to compensate for the shrinkage of the folding block components under high temperature. The folding blocks are fixed with “H-shaped” and “angle iron” anchors and reinforcing bars .