Table of Contents
Anchor-Tech Ladle Insulation Solutions
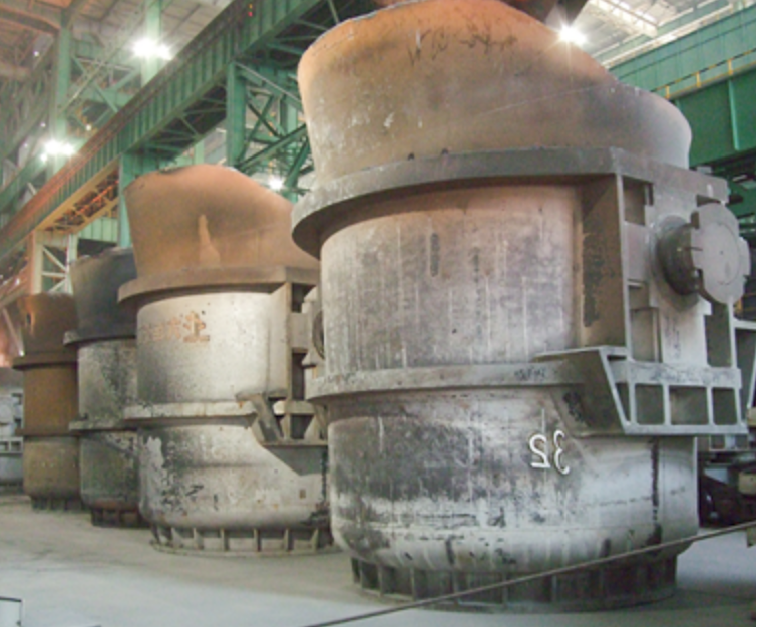
Ladle Overview
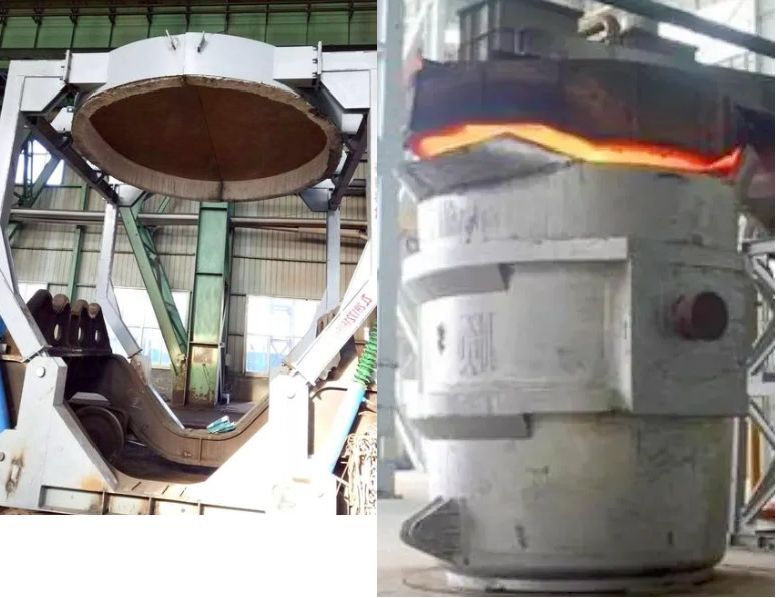
1. Purpose of the ladle
The ladle is a casting equipment and pouring equipment. It is used for pouring operations in the foundry workshop. It receives the molten iron in front of the furnace and then transports it to the casting mold by a crane for pouring.
2. Classification of ladles
According to the workshop where it is used, it can be divided into ladles for ore-fired furnace workshops and ladles for refining furnace workshops; according to the ladle wall material, it can be divided into cast steel ladles and brick-built ladles.
3. Ladle lining
The ladle lining plays a vital role in reducing heat loss of molten iron and improving its quality .
2. Anchor -Tech Ladle Insulation Structure
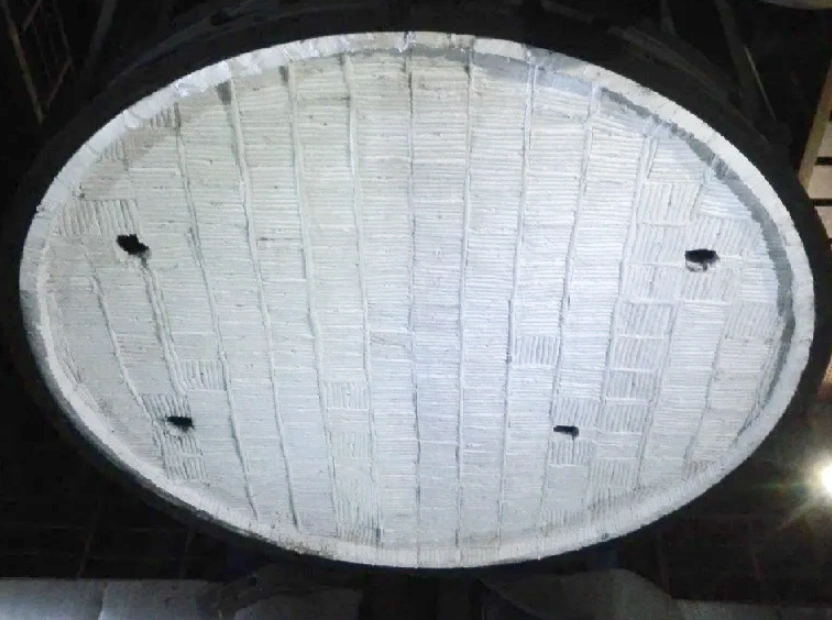
The insulation of the ladle mainly includes the ladle wall and the ladle cover.
Traditional ladle insulation
The traditional lining of the ladle wall is made of refractory bricks and castables, which results in large heat loss, increasing the combustion cost and reducing the quality of the molten iron, resulting in unsatisfactory results.
New insulation structure
The use of Anchor-Tech nanoplates is a revolution in steel ladles and iron ladles. Taking a 60-ton iron ladle as an example, after adding 20mm nanoplates to the ladle wall backing, the temperature drop of the molten iron per hour dropped from 60 degrees to 20 degrees, an overall increase of 200 degrees compared to the previous temperature drop .
The insulation of the cover is usually lined with refractory ceramic fiber. The common structure is 180mm thick zirconium-containing ceramic fiber module + 30mm thick flat blanket , and the overall insulation thickness is 200mm .
3. Advantages of using ceramic fiber for ladle insulation
1. Reduce heat loss in the ladle, thereby reducing liquid metal crusting ;
2. Significantly increase the inner wall temperature of the ladle and save energy;
3. The change of the ladle lining structure reduces the thickness of the ladle insulation layer, which is conducive to increasing the volume of the ladle;
4. It is beneficial to reduce the temperature of the outer wall of the ladle, reduce the deformation of the ladle, and extend the service life of the ladle ;
5. The outer shell temperature of the ladle can be reduced by 20℃~60℃, reducing heat radiation and improving the working environment of workers.