Table of Contents
Anchor-Tech Tunnel Kiln Full Ceramic Fiber Flat Ceiling Sectional Insulation Solution
1. Brief Introduction of Tunnel Kiln
Tunnel kiln is a modern industrial kiln widely used in building materials, ceramics and refractory industries. It is a thermal equipment for continuous production. The sintering temperature of a general sintered brick tunnel kiln is between 950℃ and 1050℃ . It belongs to a low-temperature tunnel kiln, and most of them are kiln car-type tunnel kilns . The sintered brick tunnel kiln is a process of drying, preheating, firing, heat preservation and cooling the finished products and semi-finished products with the help of the heat of raw materials and fuel. Tunnel kilns are divided into drying section, preheating section, heat preservation section, firing section, heat preservation section and cooling section according to the production process.
2. Selection of insulation materials for tunnel kiln flat ceiling
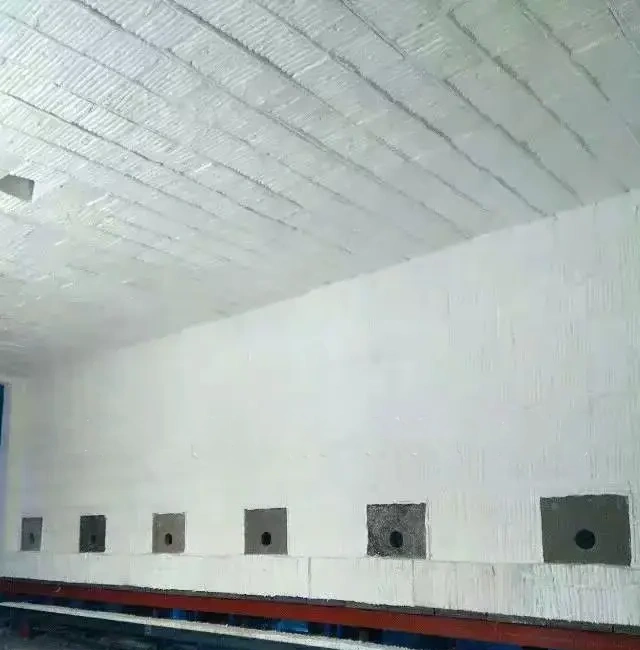
1. Material selection basis
The selection of materials for tunnel kiln roof insulation materials must comprehensively consider factors such as the maximum furnace temperature, the use conditions of ceramic fiber materials, the operating atmosphere in the kiln, the positive and negative pressure of the furnace gas in the furnace, etc. The same type of ceramic fiber material has different use temperatures due to different use conditions (type of furnace heat source, furnace gas composition and flow rate, furnace operation system). The rule is:
The same material is used at a temperature 50~100℃ higher in an electric furnace than in a gas furnace and 150~200℃ higher than in an oil furnace .
The operating temperature of the same material in oxidizing or neutral furnace gas is 100~150℃ higher than that in reducing furnace gas and dust and slag containing sulfur and low melting point oxides.
The same material can be used at a temperature 50°C lower in a continuous furnace than in a batch furnace.
2. Tunnel kiln segmented material selection:
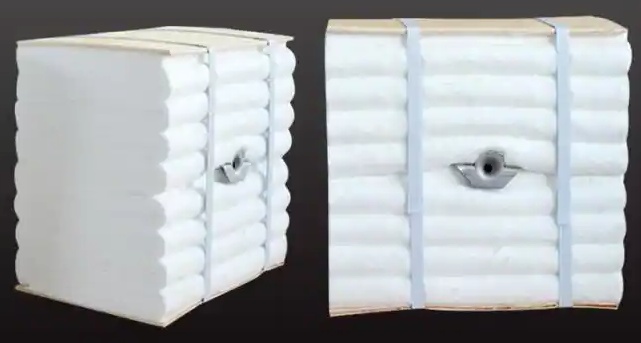
01. Preheating section
When the bricks enter the preheating section of the tunnel kiln, they continue to heat up, gradually increasing from room temperature to 600°C. This is mainly to remove moisture from the bricks. This section uses standard ceramic fiber modules with a maximum long-term operating temperature of 1050°C and a thermal insulation thickness of 350mm.
02. Insulation section
In the range of 600–900℃. There is a heat preservation section before and after the firing section. Because it is close to the firing section, for safety reasons, this section uses a high-purity ceramic fiber module with a maximum long-term working temperature of 1100℃ and a heat preservation thickness of 350mm.
03. Firing section
At 900℃~1050℃, the solid phase reaction continues, and the particles undergo high temperature changes such as melting, crystallization, and sintering. This section uses high-purity ceramic fiber modules with a maximum long-term operating temperature of 1100℃ and a thermal insulation thickness of 350mm.
04. Cooling section
The finished product can be cooled from 600℃ to room temperature without cracking. This section uses standard ceramic fiber modules with a maximum long-term operating temperature of 1050℃ and an insulation thickness of 350mm.
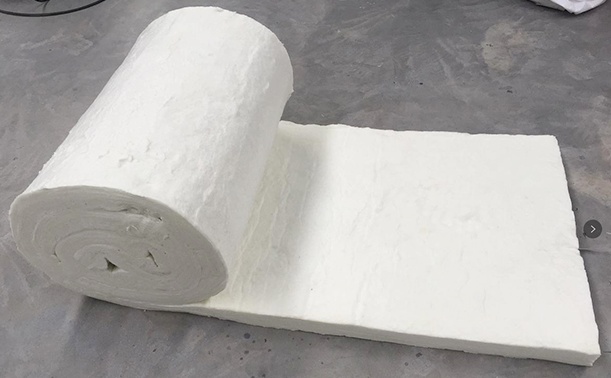