Application of Ceramic Fiber in Insulation Pits
Table of Contents
What are Insulation Pits
Insulation pits are essential auxiliary facilities in steel mills used primarily to reduce the temperature loss of hot billets. The surroundings of the insulation pit consist of a bottom plate made of reinforced concrete and pad irons. The pit walls are lined with protective railings and insulated with heat-insulating materials. Each pit is equipped with eight steel cover plates for insulation, each with a lifting ring that can be clamped for hoisting. The insulation pits measure 10 meters in length, 6 meters in width, and 1 meter in depth, accommodating two stacks of slab ingots per pit, totaling 15 pieces per stack. When six pits are filled, they can hold up to 2500 tons of hot billets, sufficient for a rolling shift.
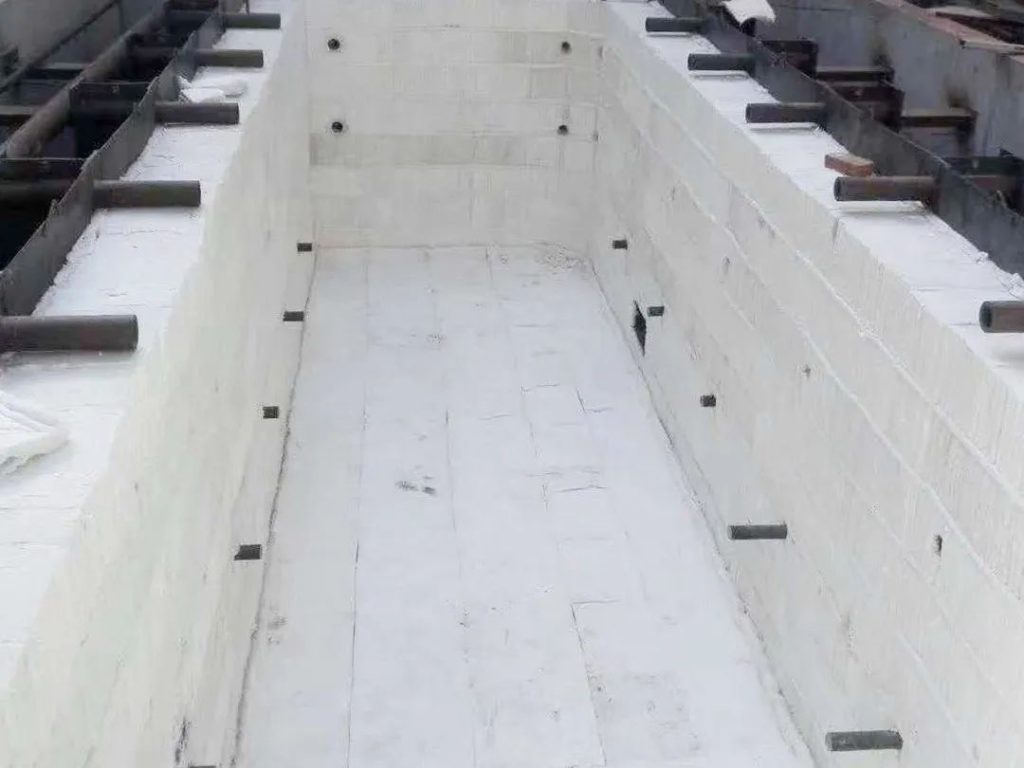
Role of Insulation Pits
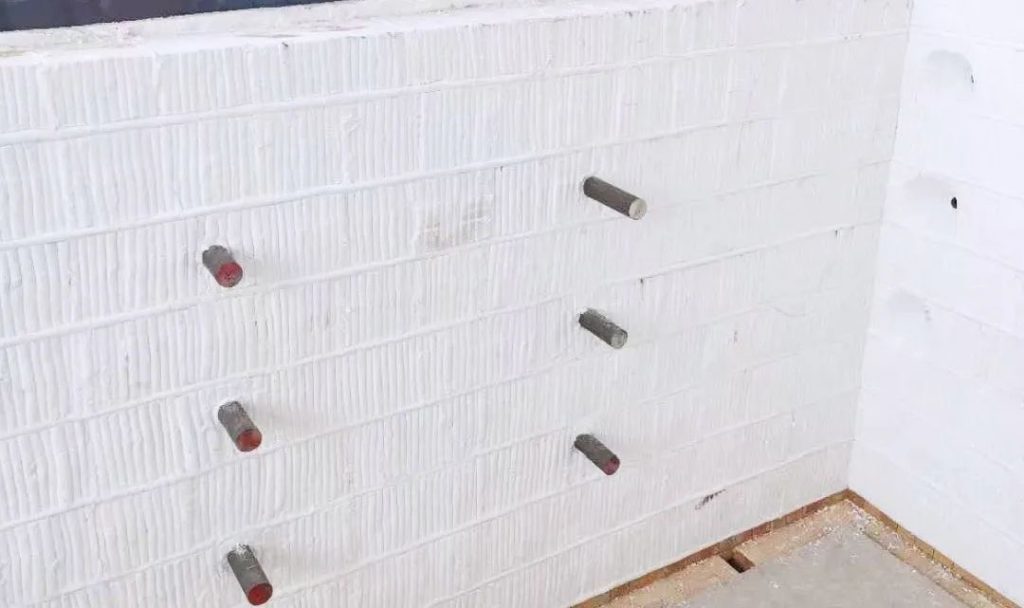
The higher the temperature at which slabs are loaded into the furnace, the better the uniformity of the heating temperature. Rapid heating reduces the preheating time of the billets, decreases burning loss and oxidation, improves the yield, and conserves metal consumption.
Given that the purpose of insulation pits is to reduce the heat loss of hot billets, the lining material of these pits requires excellent insulation and refractory properties.
Application of Ceramic Fiber Products in Insulation Pits
Lightweight refractory linings made of ceramic fibers are the optimal choice for insulation pits.
Insulation pits generally utilize an all-ceramic fiber structure, with standard ceramic fiber blankets laid as the base and high-purity ceramic fiber modules used as the hot face layer, with a total thickness of 200 to 250mm.