Application of Ceramic Fiber in Metallurgical and Mechanical Industry Furnaces
Table of Contents
Ceramic fiber, also known as aluminum silicate fiber, is a refractory material specifically designed for various high-temperature, high-pressure, and wear-prone environments. It boasts several advantages such as lightweight, high-temperature resistance, low thermal conductivity, excellent insulation properties, non-toxicity, among others.
Its outstanding characteristics make ceramic fiber products widely applied in industries such as chemical engineering and metallurgy, playing a significant role in promoting energy efficiency and emission reduction. Today, let’s explore the application of ceramic fibers in furnaces within the metallurgical and mechanical industries, aiming to assist in selecting appropriate refractory materials for industrial furnaces!
Reheating Furnaces
Reheating furnaces are used in primary rolling mills to heat steel ingots to the required temperature before rolling. These furnaces, which are pit-shaped, operate at temperatures of 1200–1250°C for heating steel ingots and 1350–1400°C within the furnace chamber, falling under cyclic thermal processes. Traditional reheating furnaces use refractory bricks. Ceramic fibers can be utilized as permanent insulation layers on the cold surfaces of the furnace wall, seal slots on the movable furnace cover (replacing the original sand sealing slots), and as insulation in the heat exchange chamber.
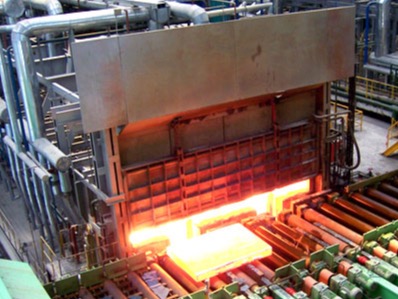
Pusher-Type Continuous Heating Furnaces
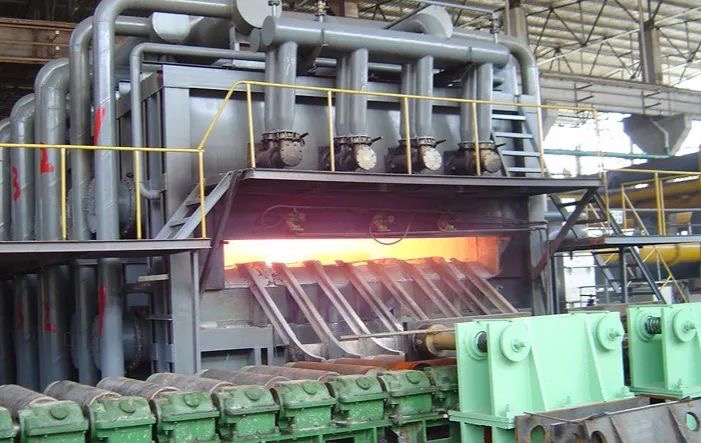
Steel ingots produced in steel mills are heated in reheating furnaces in primary rolling mills to form various shapes and sizes of initial billets (slabs, square billets). Pusher-type heating furnaces are used to reheat these billets or continuous castings to the required temperature for hot rolling. These furnaces come in two-stage, three-stage, or multi-point heating designs. Ceramic fibers are generally used as lining materials for the preheating section, insulation for the heating and homogenizing sections, lining materials for the flue system, and wrapping materials for the hot air ducts.
Walking-Beam Heating Furnaces
Walking-beam furnaces are mechanized furnaces that rely on specialized mechanisms to move steel billets within the furnace. The steel billets move back and forth on a rectangular track via movable beams on the furnace bottom, progressing from the feeding end to the discharge end. Ceramic fibers are usually used as lining materials for the preheating section, insulation for the heating and homogenizing sections, lining materials for the flue system, and wrapping materials for the hot air ducts.
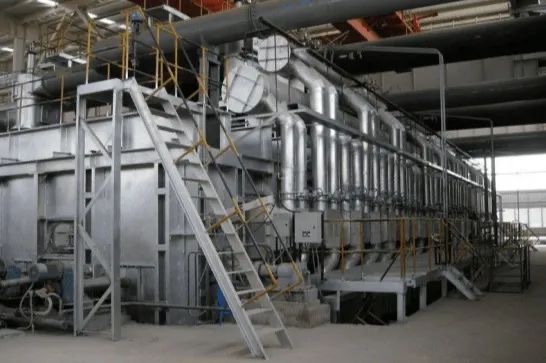
Ring-Type Heating Furnaces
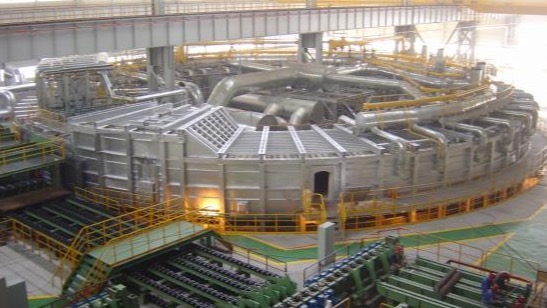
Ring-type heating furnaces, also continuous-type furnaces, consist of a circular furnace chamber and a rotating furnace bottom. They are primarily used to heat round steel billets and other shaped billets (such as wheel rims), occasionally square billets. These furnaces are commonly used in pre-heating steel for forging and before rolling and are also utilized for heat treatment purposes. As the internal walls of ring furnaces expand when heated, there is a risk of brick collapse; thus, the use of ceramic fiber modules corresponding to different temperatures is adopted for constructing a full ceramic fiber lining.
Trolley Furnaces
Car bottom furnaces belong to intermittent temperature-changing furnaces, where the furnace chamber is not partitioned, and the furnace temperature changes according to a predetermined heating schedule. These furnaces are used for preheating steel ingots (or billets) before forging or for heat treating workpieces. Traditional heavy refractory materials used in these furnaces result in high heat dissipation and heat storage losses, leading to low thermal efficiency, approximately 15%. However, with ceramic fiber lining materials and automated control, the car bottom furnaces achieve an efficiency of around 40%, significantly reducing equipment investment costs and resulting in a lightweight furnace structure.
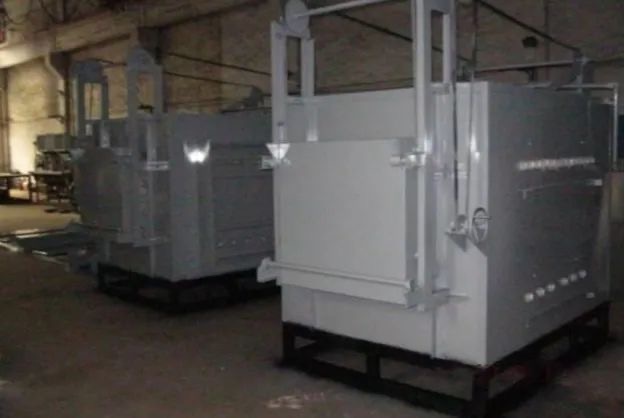
Hood-Type Furnaces
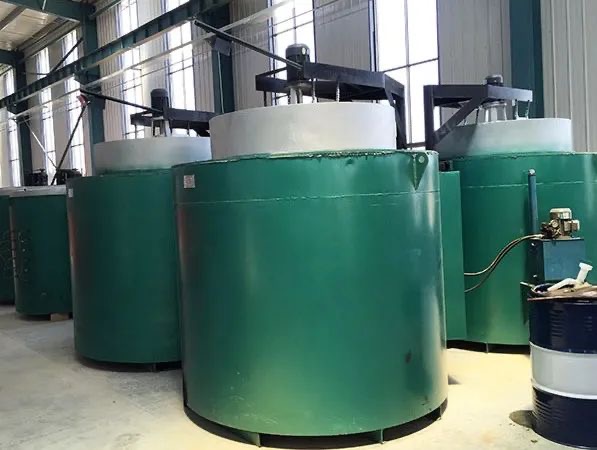
Hood-type furnaces are intermittent temperature-changing furnaces, where the furnace chamber is not partitioned, and the furnace temperature varies according to a predetermined heating schedule. They are primarily used for bright annealing of workpieces or general heat treatment. Electric resistance hood furnaces are mainly used for high-temperature heat treatment. When lightweight lining materials such as ceramic fibers are used, the weight of the external hood no longer affects the workshop’s lifting load.
Shaft Furnaces
Shaft furnaces have vertical cylindrical furnace chambers with diameters ranging from 0.5 to 4.5 meters and depths of up to 30 meters. Their thermal processes are similar to those of car bottom furnaces and are used for the heat treatment of long rod-shaped workpieces, such as gun barrels, steam turbine main shafts, generator rotors, ship diesel engine main shafts, etc. While the furnace interiors are lined with clay bricks, ceramic fibers are used as back insulation. The application of ceramic fiber modules, corresponding to various temperature zones, is used for constructing a full ceramic fiber lining in the cylindrical shaft furnace and uniformly covering the furnace top and lining.
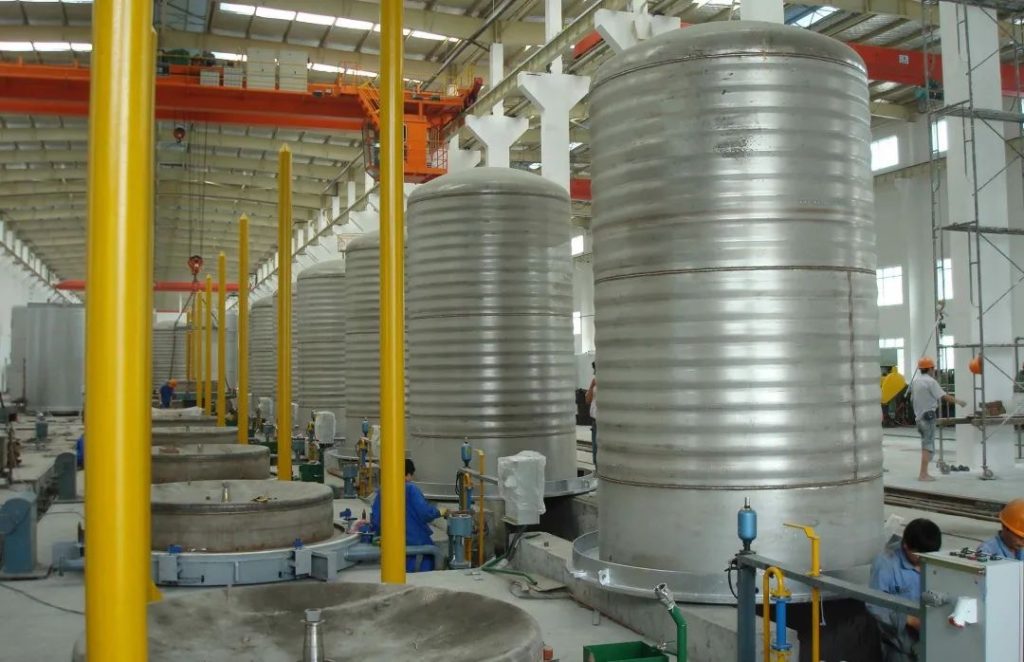