Ceramic Fiber Application in High-Temperature Insulation Scheme for Tube Furnace
Table of Contents
Introduction of Tube Furnace
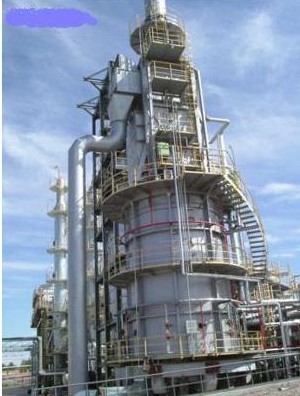
The tube furnace, also known as the tubular furnace, is widely used in petroleum and chemical production. It consists of tube arrays or coils inside the furnace, where the heat generated from burning fuel is transferred to materials within the tubes. The tube furnace usually has tube arrays or coils along the four walls and the top of the combustion chamber, initiating radiant heat transfer inside the combustion chamber. To improve thermal efficiency, a separate convection chamber is installed outside the radiant chamber, primarily for convective heat transfer. For enhanced convective heat transfer, finned tubes or spike tubes are commonly used.
Main Advantages of Tube Furnace:
High heating temperatures (up to approximately 1000℃); high heat transfer capacity and ease of operation and management. In recent years, it has rapidly developed and become one of the essential devices in modern petroleum and chemical production.
Tube Furnace Structure:
Typically consists of a radiant chamber, a convection chamber, a waste heat recovery system, a burner, and a ventilation system, among other components.
Classification of Tube Furnace:
There are various types of tube furnaces based on different classification methods. When classified by the shape of the radiant chamber, there are cylindrical furnaces, vertical furnaces, box furnaces, and platform furnaces, among others.
Refractory Material for Tube Furnace Lining
Ceramic fiber lining structures are widely used in large-scale petrochemical equipment tube furnaces. Ceramic fiber refractory materials are a new type of refractory material developed in recent decades. They have overcome the brittleness inherent in refractory bricks and monolithic refractories, thus rapidly expanding their application scope.
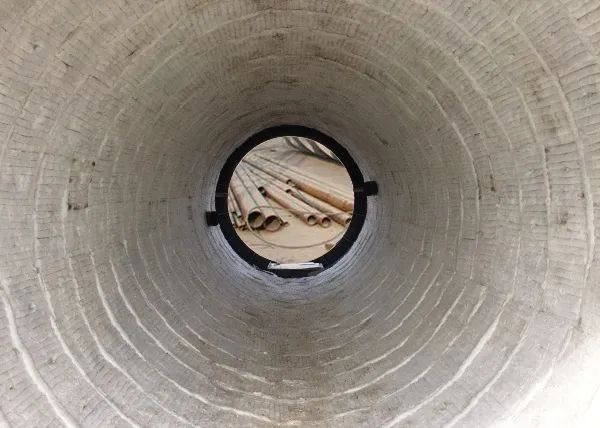
Advantages of Ceramic Fiber Furnace Lining:
- High-temperature resistance, excellent insulation performance, low heat storage, and achieving the thinnest and lightest furnace walls under equivalent conditions;
- Elasticity, resistance to mechanical vibration and thermal shock, excellent electrical insulation, and sound absorption properties;
- Simple structure, convenient construction, suitable for complex-shaped parts.
Material Selection for Tube Furnace Lining:
As the furnace chamber temperature typically reaches around 1000℃, high-purity ceramic fiber modules and ceramic fiber blankets can be chosen as direct flame-contacting refractory materials, with standard ceramic fiber blankets used as backing lining.
Insulation Structure of Tube Furnace Lining:
Utilize 30mm thick standard ceramic fiber blankets for flat laying, high-purity ceramic fiber modules (300mm), and compensating blankets arranged side by side and anchored with 304 fasteners. Due to internal airflow within the furnace chamber, a layer of Aladdin high-temperature coating can be sprayed on the fiber surface to protect the ceramic fibers, preventing peeling and slagging caused by airflow erosion.
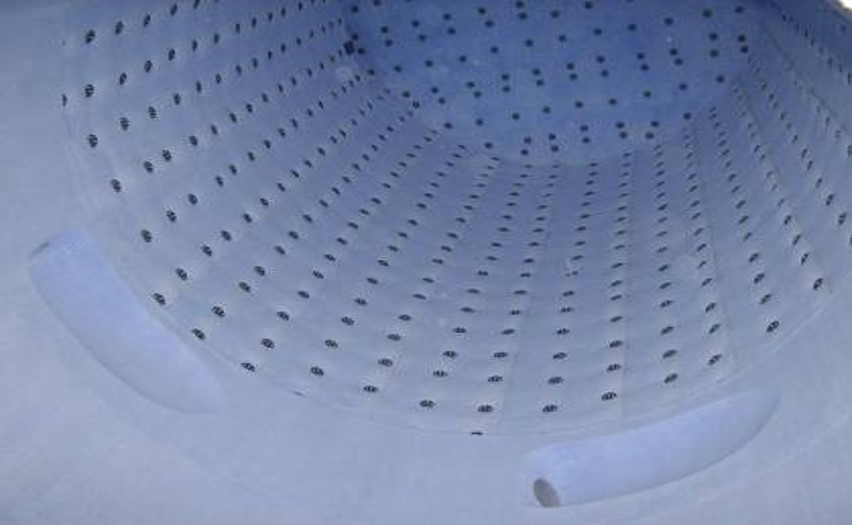