Ceramic Fiber Application in Hot-dip Galvanizing Kettle High-Temperature Insulation
Table of Contents
Description of Hot-dip Galvanizing Kettle for Zinc Plating
The term “hot-dip galvanizing kettle” typically refers to equipment used in the hot-dip galvanization process. This equipment is employed to immerse metal parts or products into molten zinc, creating a zinc coating on their surfaces to protect against corrosion and oxidation. Such equipment generally consists of a furnace used to heat and melt the zinc, as well as an immersion area for the zinc liquid to coat the metal products. This process aims to enhance the corrosion resistance and durability of metal components.
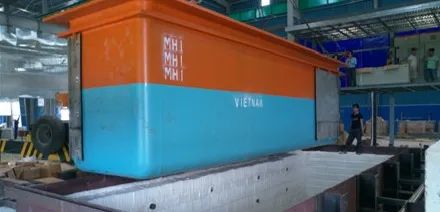
Two Heating Methods for Hot-dip Galvanizing Kettle: External and Internal Heating
Presently, the predominant method involves external heating. External heating refers to the use of a reflector furnace on one side of the zinc kettle to radiate heat onto the zinc liquid. The heat source primarily comes from burning fuel oil and gas on the reflector furnace’s zinc liquid-facing surface. Alternatively, an electric resistance band arranged on the reflector furnace’s top radiates heat onto the zinc liquid surface.
Two Insulation Methods for Zinc Kettle
For reducing the combustion intensity of the zinc kettle’s burning system, decreasing the heat transfer to the zinc liquid and maintaining the zinc liquid’s temperature above 420°C to avoid significant zinc liquid solidification, ensuring a guarantee for heating up and rapid recommissioning. This method is suitable for large interval sections where production stagnates due to insufficient task volume during hot-dip galvanizing production.
For temporary or shorter production intervals, the insulation temperature should be slightly increased to facilitate faster temperature elevation within a shorter time, allowing for a quick reach of the required zinc liquid temperature for normal galvanizing. For instance, if the zinc liquid’s working temperature during production is set at 450°C, the insulation period should maintain the zinc liquid temperature above 430°C.
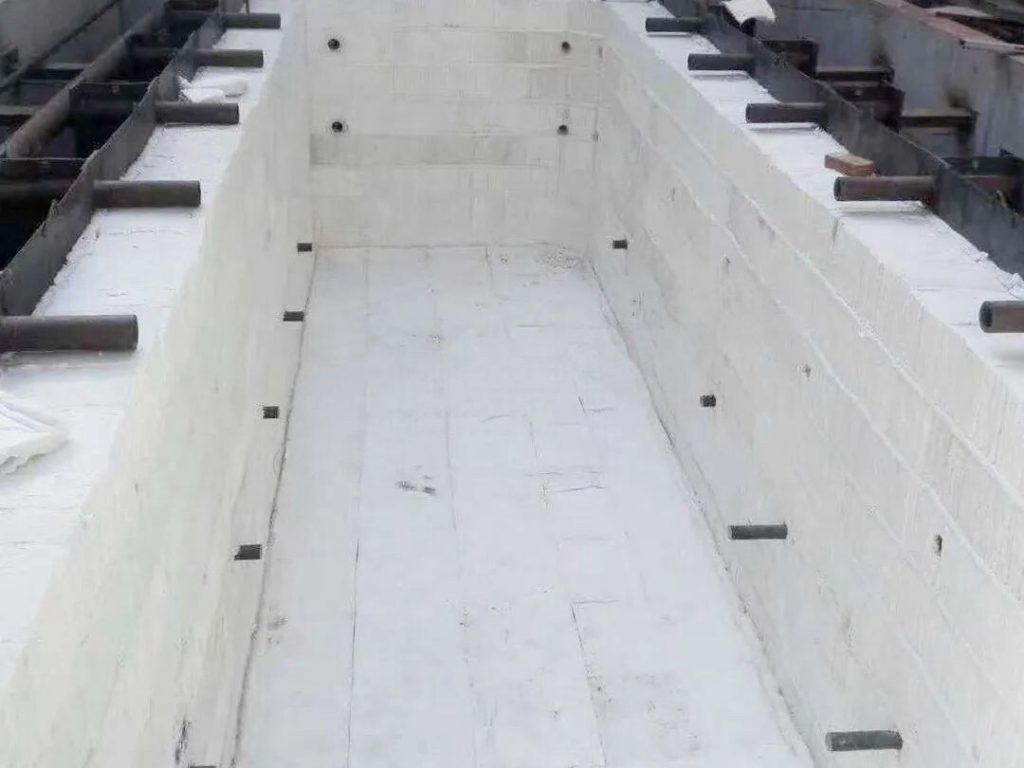
Two Heating Methods for the Zinc Kettle
Considering the zinc liquid temperature is around 450°C, the zinc kettle’s outer wall temperature is approximately 500°C. Therefore, lightweight ceramic fiber materials are chosen for insulation, providing significant thermal insulation effects. The long-term use temperature is 1000°C for the standard 1260-type ceramic fiber products.
Insulation is applied to the outer side of the zinc kettle’s fire passage, including the sidewalls and top cover plates of the zinc kettle. A method involves laying two layers of 30mm thick ceramic fiber blankets (compressed to 50mm thickness), followed by using 250-300mm thick ceramic fiber modules, resulting in a total insulation thickness of 300-350mm. An arranged staggered layout is adopted, using ceramic fiber boards at the top cover to prevent wind speeds within the fire passage from blowing and blocking ceramic fiber materials. Therefore, ceramic fiber boards are used for insulation at the top, generally employing two layers of 50mm thick ceramic fiber boards staggered and jointed.
Advantages of Ceramic Fiber in Zinc Kettle Insulation
Chemical Stability
In the hot-dip galvanizing kettle, the insulation materials must endure high-temperature oxidation and corrosion caused by the zinc liquid’s corrosive conditions. Ceramic fiber modules and blankets, being inorganic non-metallic materials, exhibit exceptional chemical stability, less affected by the combustion atmosphere within the zinc kettle’s insulation layer.
Excellent Thermal Shock Resistance
The lightweight high-temperature resistant ceramic fiber module lining in the zinc kettle insulation possesses outstanding rebound properties. Pre-compressed ceramic fiber modules, when installed and unpacked, instantly form an airtight and integral refractory layer without the need for expansion joints.
Lightweight andOutstanding insulation performance
Special ceramic fiber modules for zinc kettle insulation, along with ceramic fiber blankets, weigh only 1/10 of traditional refractory materials such as fire bricks and castables. This significantly reduces the weight load on the zinc kettle insulation structure and lowers the project cost for hot-dip galvanizing kettle insulation.