Ceramic Fiber Insulation Scheme for Coke Oven Cover
Table of Contents
Overview of Insulation for Coke Oven Cover
The coke oven cover refers to the covering structure at the top of the coke furnace (coking stove). A coke oven is a device used to heat coal or other raw materials at high temperatures to produce coke. The cover is placed on top of the coke furnace to seal the chamber, maintaining the high-temperature and high-pressure environment inside. Its design and structure prevent the leakage of gases produced within the furnace, ensuring the effective heating and combustion processes inside the coke furnace. Its structure mainly includes the cover body, sealing plates, insulation materials, and guiding devices for the cover. The main forms of coke oven covers include square and circular covers.
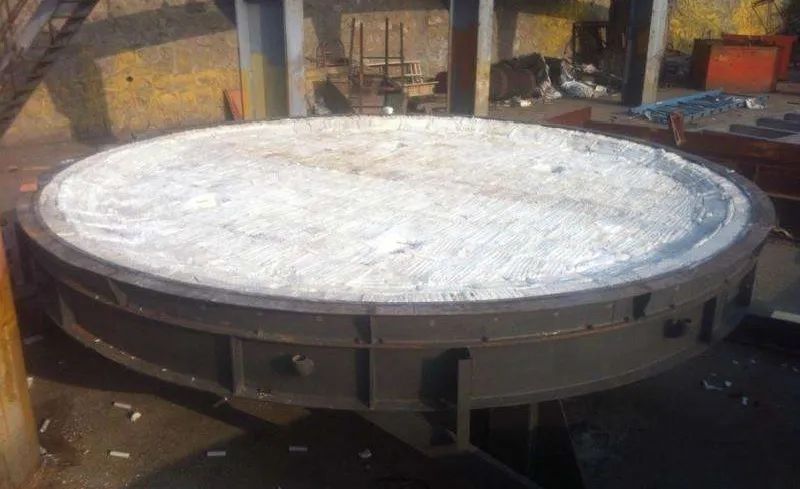
Temperature for the Insulation of Dry Quenching Coke Oven Cover
The coke flow process involves pushing red-hot coke at around 1100℃ out of the coking chamber. The long-term working temperature of the coke oven cover is 1100℃, generally not exceeding 1200℃. To avoid delay in equipment use due to insulating material and extend the working life of insulation material, in most cases, Anchor Technology recommends using their 1400 Anchor Technology Ceramic Fiber Zirconia Module + 1400 Anchor Technology Ceramic Fiber Zirconia Blanket and 1400 Anchor Technology Ceramic Fiber Zirconia Board for lightweight insulation layer.
Ceramic Fiber Insulation Structure for Coke Oven Cover
In the early stages, the refractory insulation material for the dry quenching coke oven cover was fixed using a stainless steel mesh. However, in practical applications, the stainless steel mesh tends to oxidize and fall off, causing the dry quenching tower to become unusable. By fixing the Anchor Technology ceramic fiber zirconia module with bolts inside the insulation material, leaving a distance from the hot surface, the problem of high-temperature oxidation is resolved. Ceramic fiber materials are primarily applied to the bottom of the coke oven cover, which is the side in contact with the coke furnace.
The current preferred refractory material for the coke oven cover is the ceramic fiber zirconia module with a classification temperature of 1400℃. The predominant size used is 300x300x200/180mm, with edge areas being 150×180/200*150mm. The actual dimensions can be customized as per requirements, with supporting 310S stainless steel anchoring fittings.
Composite Furnace Lining Structure of Insulation Layer for Coke Oven Cover
- Insulation Layer: Total thickness of 200mm/180mm/150mm
- Backing Layer: Anchor Technology’s ceramic fiber zirconia blanket, thickness of 20mm
- Hot Surface: Anchor Technology’s ceramic fiber zirconia module, thickness of 180mm/150mm
- Ceramic Fiber Surface: Coated with a layer of Anchor Technology’s high-temperature curing agent
- Arrangement: Utilizes a “parallel” arrangement
- Interlayer Compensation Blanket: Anchor Technology’s ceramic fiber zirconia blanket, fixed with “U”-shaped heat-resistant steel nails
Regular Maintenance of Coke Oven Cover
The insulating materials for the coke oven cover use module installation with a density of 220kg/m3, fully complying with the relevant parameters specified in GB/T3003-2017. Newly installed modules are comparatively soft, as their internal fibers are filled with a significant amount of air, achieving effective insulation. After use, due to the high-temperature flame and a large amount of smoke and sulfurization reactions, the insulating material gradually hardens, leading to decreased insulation efficiency, with an approximate lifespan of three years. To ensure better insulation efficiency for the coke oven cover, it is recommended that customers apply Anchor Technology’s high-temperature surface curing agent for surface protection every six months or replace Anchor Technology’s ceramic fiber module annually.
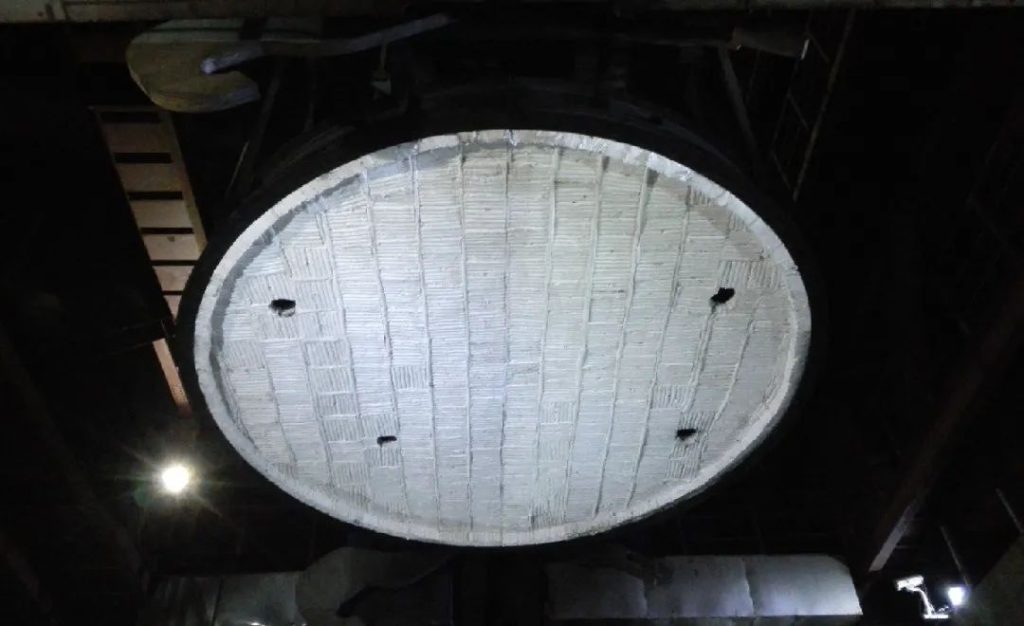