Ceramic Fiber Insulation Scheme for Potassium Sulfate Reaction Furnace
Table of Contents
I. Overview of Potassium Sulfate Reaction Furnace
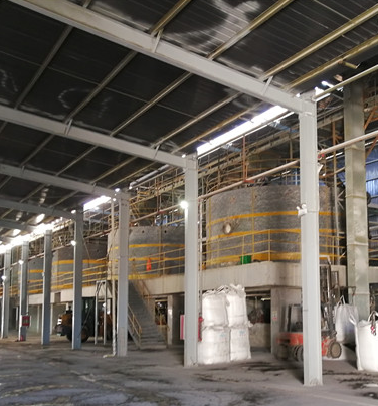
Potassium sulfate is a major chloride-free potassium fertilizer in agriculture. The Mannheim process is a method of producing potassium sulfate using potassium chloride and sulfuric acid as raw materials, and the current production process is mature. Its advantages are as follows: the obtained product potassium sulfate has a high grade (W(K20) 50%~51%), with almost no losses, and a relatively high yield of potassium. Therefore, the potassium sulfate reaction furnace is also known as the Mannheim furnace.
Insulation of the potassium sulfate reaction furnace: The furnace consists of a combustion chamber (heating chamber), reaction chamber, flue, stirring rake, burners (two), feeders, discharge ports, etc. The potassium sulfate furnace reaction chamber is located below the combustion chamber, and the flue is below the reaction chamber. The heat generated in the combustion chamber is radiated to the materials in the reaction chamber, and the residual heat in the flue is fully absorbed by the reacting materials.
- The reaction temperature of the potassium sulfate reaction furnace is controlled at around 550°C.
- Mid-section temperature of the potassium sulfate reaction furnace reaction chamber: 550-600°C;
- Top temperature of the potassium sulfate reaction furnace: ≤920°C
- Bottom temperature of the potassium sulfate reaction furnace: ≤650°C
- Inlet pressure of the combustion chamber of the potassium sulfate reaction furnace: Slight negative pressure
- Pressure in the reaction chamber of the potassium sulfate reaction furnace: Slight negative pressure
II. Insulation Scheme of Potassium Sulfate Reaction Furnace
Insulation structure of the potassium sulfate reaction furnace (Mannheim furnace) with ceramic fiber lining: 1400 type zirconia ceramic fiber modules + 30mm 1400 type high-alumina ceramic fiber blankets.
Insulation thickness of the ceramic fiber lining for the potassium sulfate reaction furnace (Mannheim furnace): 300mm
Considering that there is a certain flue gas scouring between the potassium sulfate reaction kettle and the shell, it will cause some corrosion to the potassium sulfate reaction kettle. Anchor-Tech ceramic fiber modules are coated with Anchor-Tech high-temperature curing agent twice, which can resist corrosion and high wind speeds.
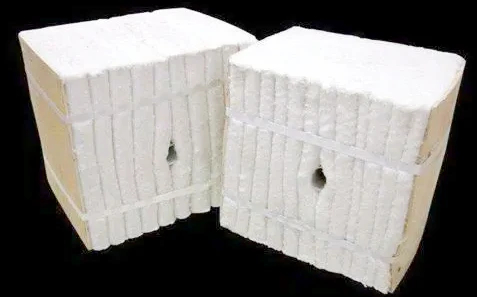
III. Installation Method of Insulation Materials for Potassium Sulfate Reaction Furnace
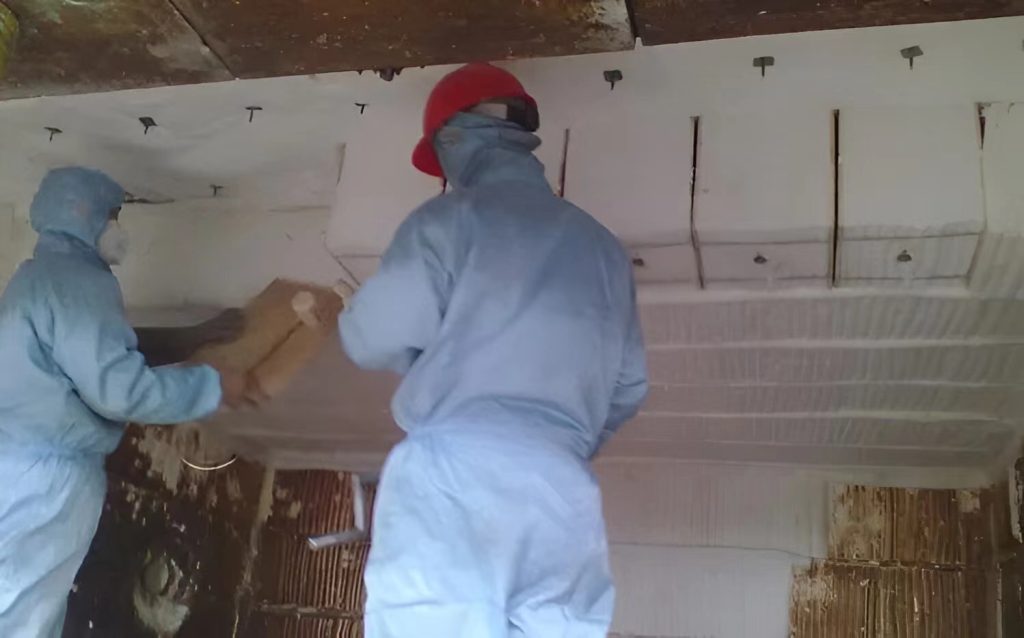
The installation method of ceramic fiber modules adopts a “parallel” arrangement.
Arrange along the compression dimensions of the ceramic fiber modules. The gaps between ceramic fiber module rows are compressed with a layer of 20mm-thick folded ceramic fiber blanket, and “U”-shaped nails are inserted at intervals of 500~700mm to fix them on the ceramic fiber modules to compensate for the possible shrinkage of the unexpanded fiber surface.
This structure can avoid the occurrence of “flowering” caused by uneven expansion of the fiber modules at the corners in the “parquet floor” arrangement method, achieving good insulation effects.
During the installation of the backing layer at the top of the furnace, quick clips are used along with the modules and temporarily fixed with bolts.