Table of Contents
Ceramic fiber insulation solution for heating furnace lining in refinery
1. Refinery Overview
An oil refinery refers to a factory that produces diesel, gasoline, kerosene, lubricating oil, petroleum coke, asphalt, ethylene and other products through processes such as distillation, catalysis, cracking, pyrolysis and hydrotreating of crude oil extracted from the ground.
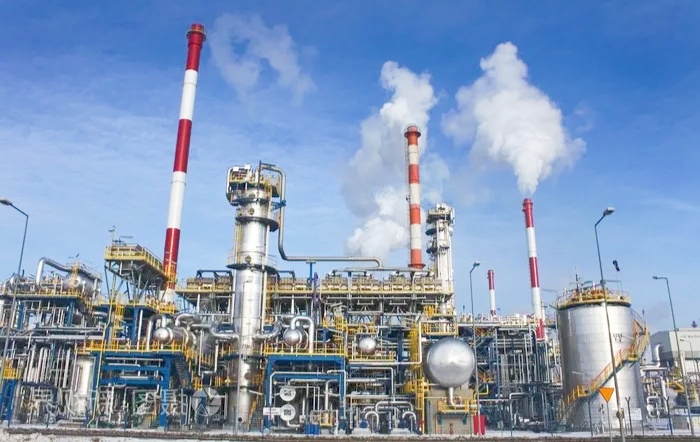
2. Characteristics of Ceramic Fiber Lining for Refinery Heating Furnace
(1) Except for the wall-mounted combustion furnace type, the furnace wall, furnace top and transition flue of other furnace types adopt full fiber structure;
(2) The furnace temperature of the hydrogen production reformer is about 1150 degrees, and the furnace temperature of other heating furnaces is 800-900 degrees;
(3) The full fiber furnace lining can use Anchor-Tech high-aluminum ceramic fiber module, and the backing blanket can use Anchor-Tech standard ceramic fiber blanket ;
(4) Special-shaped parts include fire holes, explosion-proof doors, removable doors, etc.;
(5) The furnace bottom can basically be made of refractory bricks + backing board Anchor-Tech standard ceramic fiberboard
3. New ceramic fiber anti-corrosion and thermal insulation lining structure
(1) When the sulfur content of the fuel is ≥10 mg/kg, the lining structure is: anti-dew point corrosion coating + ceramic fiber blanket + aluminum silicate fiber module
(2) When the sulfur content of the fuel is ≥500 mg/kg, the lining structure is: anti-dew point corrosion coating + ceramic fiber blanket + stainless steel foil + ceramic fiber module
( 3) External wall temperature ≤70℃ (or ≤60℃) Energy-saving lining: Fiber lining Structure: Ceramic fiber blanket + microporous nanoplate + ceramic fiber blanket + ceramic fiber module