Ceramic Fiber Insulation Solution for Pusher-Type Heating Furnace
Table of Contents
Introduction to Pusher-Type Heating Furnace
The pusher-type continuous heating furnace is a thermal equipment that reheats various carbon-formed products, such as plate materials, large steel ingots, small steel ingots, or continuous casting billets, to the required temperature for hot rolling. Based on thermal principles, temperature requirements, and furnace structure, the heating furnace can be divided into two-stage, three-stage, or multi-point heating types.
Structure of Two-Stage Pusher-Type Heating Furnace
The two-stage pusher-type heating furnace can be divided longitudinally into preheating and heating sections. The furnace has a useful length of about 20,000 meters, an internal width of 3,700 mm, and an arch thickness of approximately 230 mm. The preheating section operates at a temperature of 1,100°C and can use refractory fiber as wall lining material. The insulation layer of the heating section can use refractory fiber material.
Structure of Three-Stage Pusher-Type Heating Furnace
The three-stage pusher-type heating furnace can be divided internally into preheating, heating, and equalizing temperature zones. Usually, it has three heating points: upper heating, lower heating, and equalizing temperature segments. The preheating section uses waste gas as a heat source with temperatures between 850-950°C, not exceeding 1,050°C. The heating section maintains temperatures between 1,320-1,380°C, while the equalizing section maintains temperatures between 1,250-1,300°C.
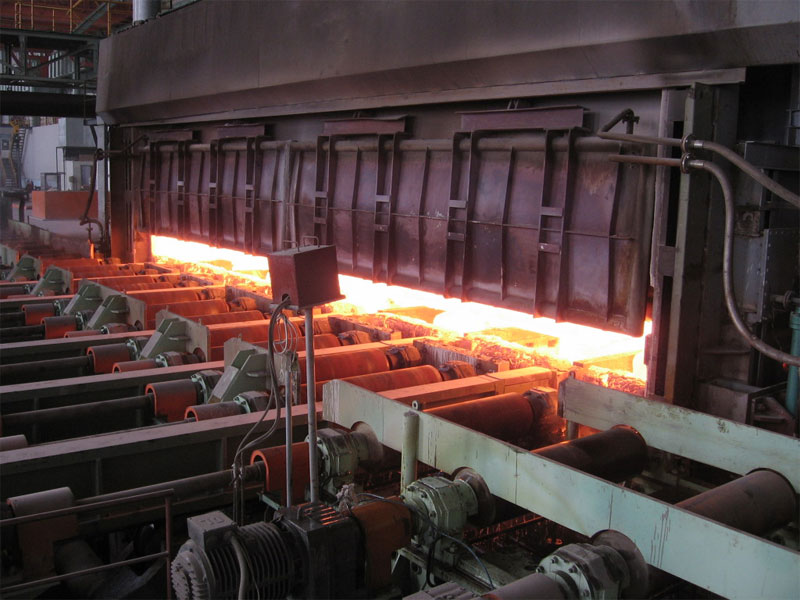
Recommended Furnace Lining and Insulation Thickness:
A. Material: Considering the temperature distribution inside the heating furnace and the environmental atmosphere, high-purity and zirconium-containing products are recommended for the lining in the preheating section, while standard products are used for the lining. For insulation, high-purity and zirconium-containing ceramic fiber products are suggested.
B. Insulation Thickness: The insulation thickness in the preheating section is generally set at 220-230mm, the insulation layer of the heating section is 40-60mm, and the furnace top insulation is 30-100mm.
Recommended Furnace Lining Structure:
A. The preheating section utilizes a composite fiber lining structure with spread and stacked ceramic fiber insulation. Spread lining employs ceramic fiber blankets, welded with heat-resistant stainless steel anchoring devices, and secured with quick-release clips, typically 20-100mm thick. Stacked lining uses angle-iron-type ceramic fiber folding blocks or hanging-type refractory fiber modules. The top part adopts two layers of 30mm thick ceramic fiber needle-punched blankets (compressed to 50mm), followed by 200-250mm thick single-hole hanging fiber components.
B. The heating section employs a spread ceramic fiber blanket lining for insulation. The insulating lining uses 40-60mm thick refractory ceramic fiber blankets. The furnace top insulating layer is composed of 30-100mm thick ceramic fiber blankets or ceramic fiber boards.
C. The hot air duct can be insulated with ceramic fiber blankets or padding.
Fiber Lining Installation :
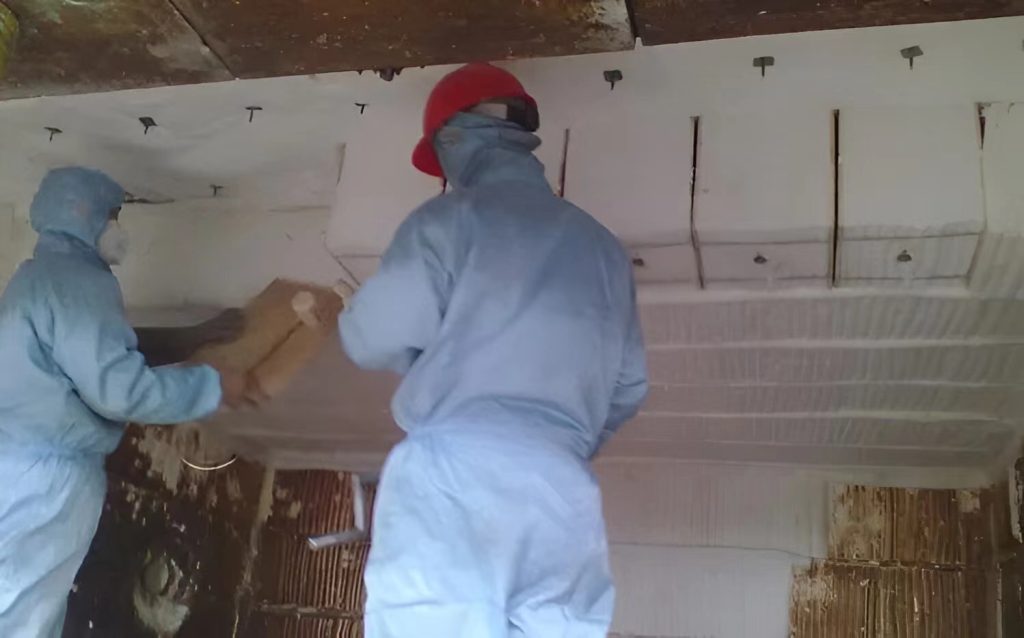