Table of Contents
Energy-saving transformation of brick factories – Anchor-Tech ceramic fiber modules
01. Brick factory production process
1) Raw material preparation
2) Raw material aging treatment
3) Extrusion molding
4) Drying and roasting
The energy consumption of a brick factory is divided into two parts: the energy consumption of raw material preparation and brick forming equipment, and the energy consumption of brick drying and sintering.
02. Energy-saving transformation of brick factory using Anchor-Tech ceramic fiber modules
The roof of traditional sintered brick tunnel kiln is mostly an arched roof or suspended flat roof built with refractory bricks, and there are also flat roofs built with prefabricated blocks of refractory castables. Refractory bricks and refractory castables are both heavy refractory materials. Compared with Anchor-Tech ceramic fiber module refractory furnace lining, they have the following disadvantages: high heat capacity, high thermal conductivity, long construction period, and complex maintenance. Heavy refractory materials need to be baked after construction, and the human factors and environmental factors of baking the furnace will directly affect the service life of the tunnel kiln. Compared with heavy refractory materials, Anchor-Tech ceramic fiber furnace lining can be put into use after installation.
In combination with the actual characteristics of the sintered brick tunnel kiln, on the basis of ensuring the safe operation of the tunnel kiln, the sintered brick tunnel kiln roof was changed to a complete set of thermal insulation construction scheme of refractory fiber module composite suspension and refractory fiber folding block “T+L” composite suspension system, which realized the lightweight of the kiln chamber wall (1/10 of heavy refractory materials), and had the characteristics of low heat storage (1/10 of heavy refractory materials), thermal shock resistance, good integrity, easy maintenance, and strong controllability of furnace temperature (stable quality of fired products).
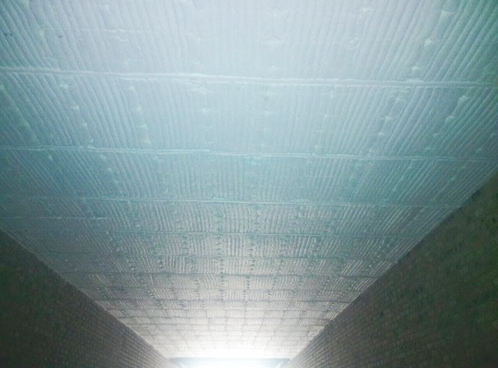
03. Introduction to Anchor-Tech Ceramic Fiber Energy Saving Module
Anchor-Tech ceramic fiber modules for energy-saving transformation of brick factories are special products that replace traditional heavy-weight ring-top refractory brick insulation structures . This product is made of long-fiber ceramic fibers of corresponding materials (determined according to different heating intervals and fired brick raw materials) through spinning and needle punching, and processed on special machinery according to the fiber component structure and size. During the processing, a certain proportion of compression (compression ratio>50%) is maintained to ensure that after the ceramic fiber module wall lining is completed, each ceramic fiber adjacent module is fully expanded and squeezed into a seamless integral ceiling sealing structure.
The Anchor-Tech ceramic fiber folding blocks for energy-saving transformation of brick factories are optimized based on traditional built-in anchors. Their characteristics are: the suspended stainless steel parts are on the outside of the kiln roof, which makes construction quicker and the structure more stable; the large-scale 600*300mm refractory folding blocks for brick factories make the kiln roof insulation joints less, with higher integrity and better energy-saving effects; maintenance is more convenient and can be operated by ordinary technicians.
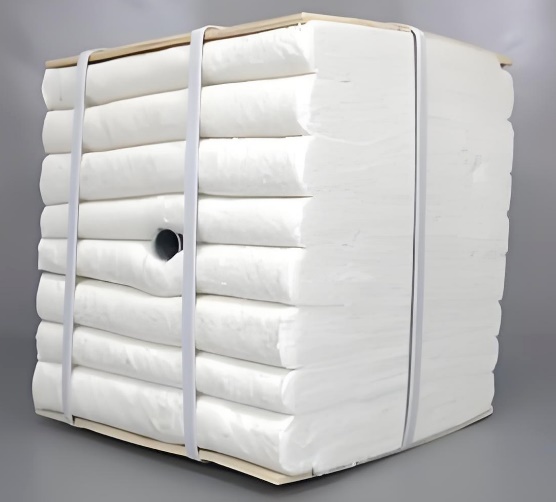