Factors Affecting the Performance of Ceramic Fiber Modules
Table of Contents
Ceramic fiber modules are formed by the natural settling of loose ceramic fibers on a collector belt, creating a uniform fiber blanket. This blanket is then processed through a needle-punching technique to obtain a binder-free needle-punched blanket, which is folded and packaged and assembled into modules. The thermal stability of ceramic fiber modules is closely related to factors such as the diameter, specific heat capacity, and density of the ceramic fibers.
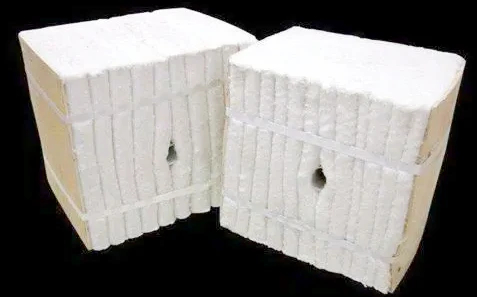
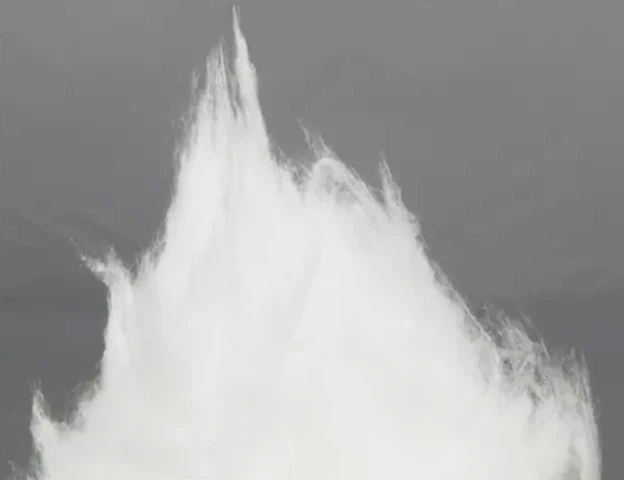
Ceramic fibers are lightweight, refractory materials with a fibrous structure. Due to their light weight, high temperature resistance, good thermal stability, low thermal conductivity, low specific heat, and resistance to mechanical vibrations, they are widely used in industries such as mechanical engineering, metallurgy, chemical engineering, petroleum, ceramics, glass, and electronics.
The key indicators in ceramic fibers are their diameter and thermal stability.
Commonly used in the ceramic industry are Al2O3 and SiO2 fibers. They are categorized into different usage ranges based on the content of Al2O3, and Cr2O3 material is introduced to enhance their refractory and oxidation resistance properties. Generally, fiber products with high aluminum oxide content and low impurity content like iron oxide appear pure white, while fibers incorporating chromium oxide exhibit a green color.
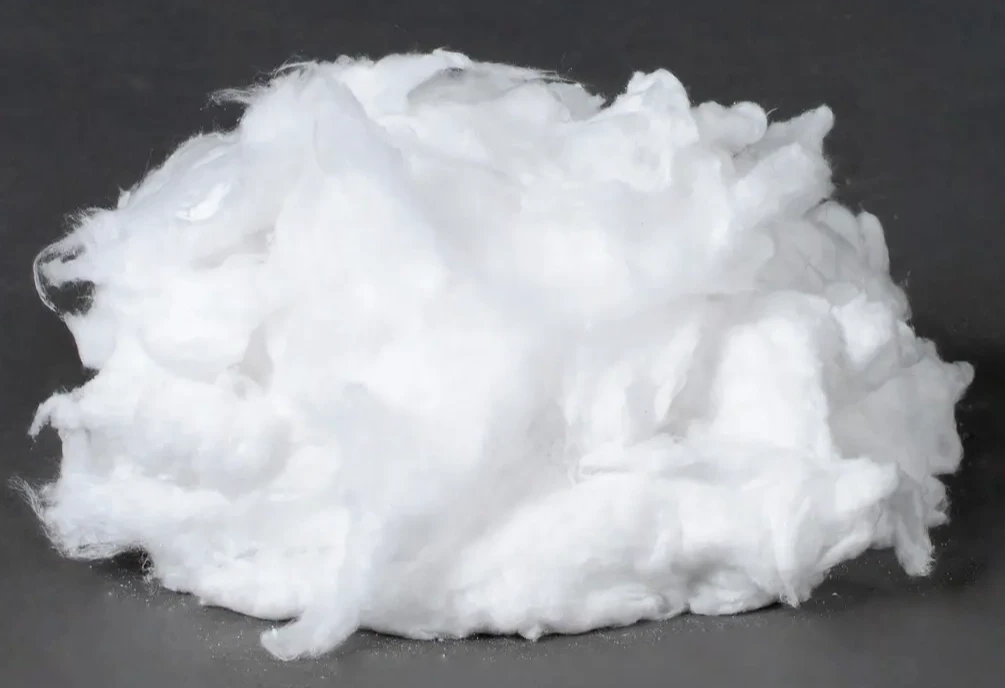
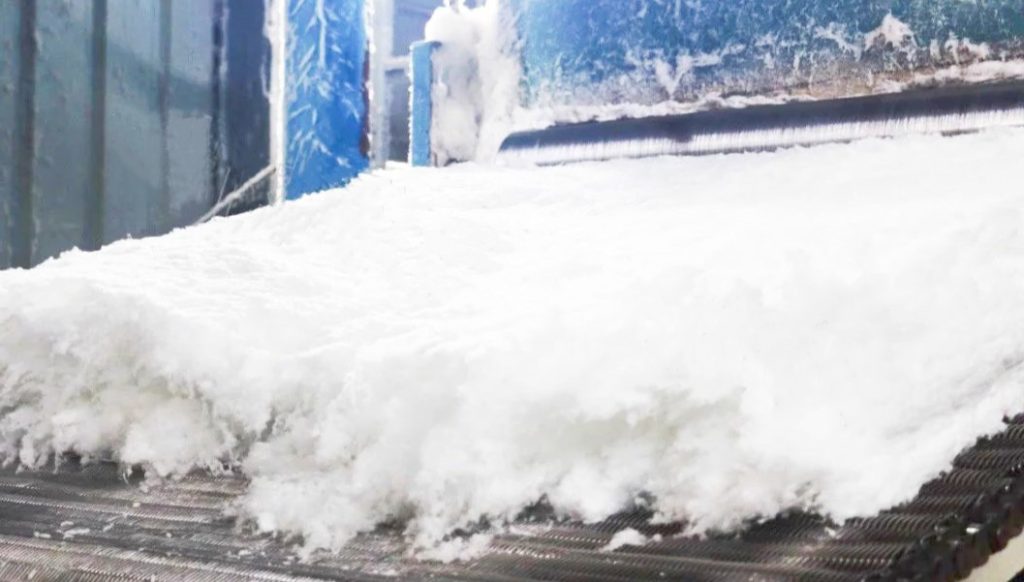
Ceramic fibers typically have diameters ranging from 2 to 5 micrometers, with lengths between 30 to 250mm. The fiber surface is smooth and cylindrical. Fibers that are finer, less dense, and have lower specific heat can be used at higher temperatures. Coarser fibers with more impurities may result in less satisfactory performance.
The thermal stability of ceramic fibers is a crucial indicator.
Various products of Al2O3 and SiO2 fibers have specific shrinkage ranges at 1260°C. The degree of shrinkage directly impacts thermal stability.
Due to the low thermal conductivity, low density, and light weight of fibers, lighter steel frame support structures are used in the design and construction of kilns, ushering in an era of “lightweight kilns”. Ceramic fibers have low heat storage capacity, making them suitable for rapid heating and cooling during firing process.
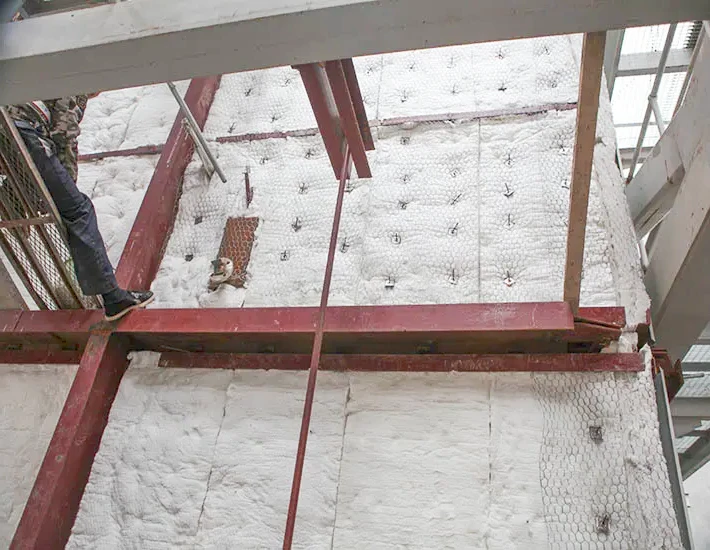
Ceramic fibers are flexible and can be processed into products with grooves or openings. They also have good resistance to mechanical vibration and impact, and exhibit relatively high chemical stability. These advantages have propelled the development of new types of kilns and played a significant role in promoting the advancement of ceramic technology and industry.