Insulation Solution for Ceramic Fiber in Hot-Dip Galvanizing Furnace
Table of Contents
Hot-dip galvanizing technology is a high-energy-consuming production process. With China advocating energy conservation, energy-saving insulation work in the hot-dip galvanizing industry has become crucial. In continuous hot-dip galvanizing production lines, the annealing furnace for hot-dip galvanizing accounts for about sixty to seventy percent of the total energy consumption. Therefore, the insulation of the hot-dip galvanizing annealing furnace is an excellent application for ceramic fiber products.
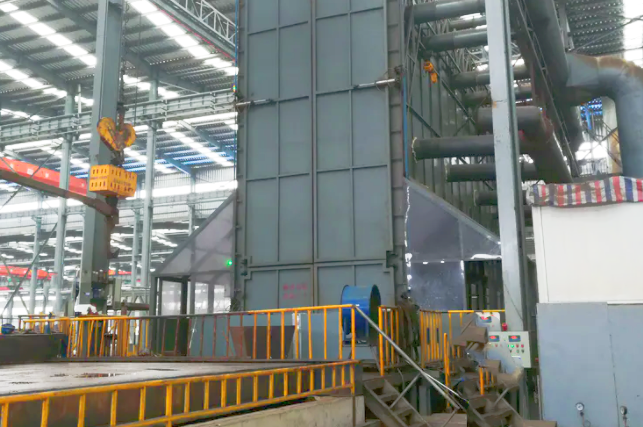
1. Insulation Solutions for Various Sections of the Hot-Dip Galvanizing Annealing Furnace
The continuous hot-dip galvanizing annealing furnace serves as the prelude to entering the galvanizing pot. It is mainly divided into the heating section, the uniform heating section, and the rapid cooling section.
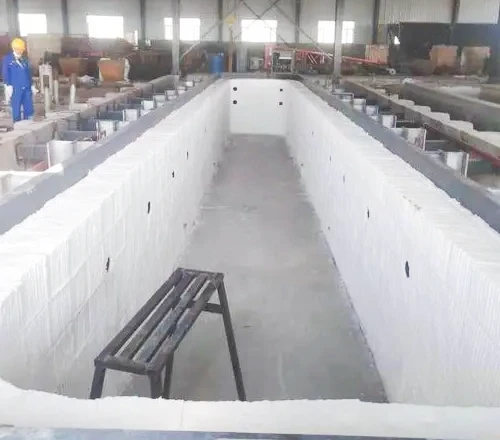
1)Heating Section
In the heating section, the primary task is the oxidation-reduction treatment of the iron plates’ surfaces. Most of this is done using gas-fired radiant tubes for heating. The temperature is kept within 1000°C. For this temperature range, standard ceramic fiber modules are mainly used for the side walls and roof. The furnace bottom is paved with refractory bricks, supplemented with calcium silicate boards.
2)Uniform Heating Section
In the uniform heating section, the heating is primarily done by resistance wire, without an open flame. The furnace bottom is also paved with refractory bricks, forming grooves for laying the resistance wires. The side walls and roof are mainly installed with ceramic fiber modules.
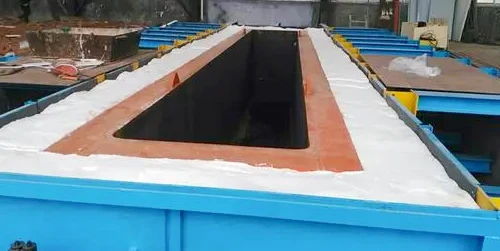
3)Rapid Cooling Section
In the rapid cooling section, which is the subsequent step before the iron plate enters the zinc pot, it is required to rapidly cool down to below 560°C. In this temperature range, high-speed fans are used to blow the iron plate, so the insulation work in this temperature range requires careful attention. The furnace side walls and roof are insulated with ceramic fiber blankets, and the furnace bottom is covered with calcium silicate board. Additionally, stainless steel plates are used to cover the inside furnace. Due to the high-speed airflow in this temperature range, placing a layer of stainless steel plates helps prevent fibers from scattering and sticking to the iron plate. It also effectively preserves the integrity of the insulation materials. For the treatment of the furnace cover in the rapid cooling section, insulation ceramic fiber cotton and stainless steel plates are used for comprehensive sealing.
2. Insulation Solution for the Hot-Dip Galvanizing Pot Section
The process of galvanizing iron plates in the zinc pot involves a heat treatment process. In the furnace used for heating the zinc pot, ceramic fiber modules are also necessary for insulation. This insulation process generally occurs in areas with high temperatures, such as near the nozzles of the furnace, or at the two ends of the zinc pot, where temperatures are kept below 1100°C. In this section, the insulation layer should be made thicker.
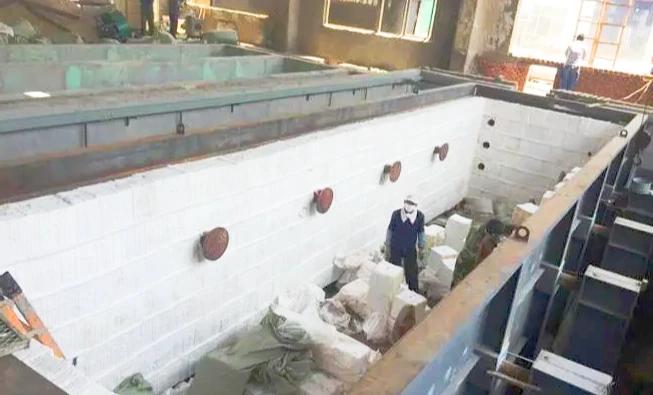
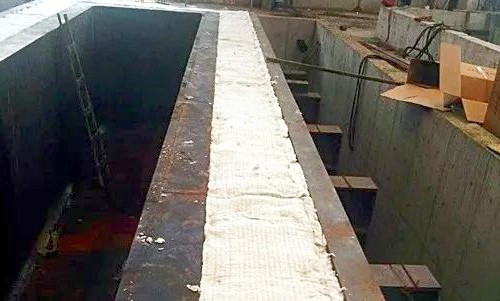
In the insulation phase of the zinc pot, most furnace companies still predominantly use ceramic fiber modules, while a small number of furnace companies opt for refractory bricks and castables. However, both the insulation performance and integrity of refractory bricks and castables are inferior to ceramic fiber products. In terms of installation and construction, ceramic fiber modules are also much more convenient compared to refractory bricks and castables.