Refractory Ceramic Fiber Lining for Flat-Top Tunnel Kiln - Insulation Solution
Table of Contents
1. Overview of Flat-Top Tunnel Kiln
The pulverized coal brick kiln is a tunnel kiln used to heat and fire wet brick blanks primarily made from coal gangue or shale, producing finished bricks. The length of a pulverized coal brick kiln is generally over 140 meters, with different widths available depending on the size of the kiln, including 3.3 meters, 3.6 meters, 4.6 meters, and 6.9 meters.
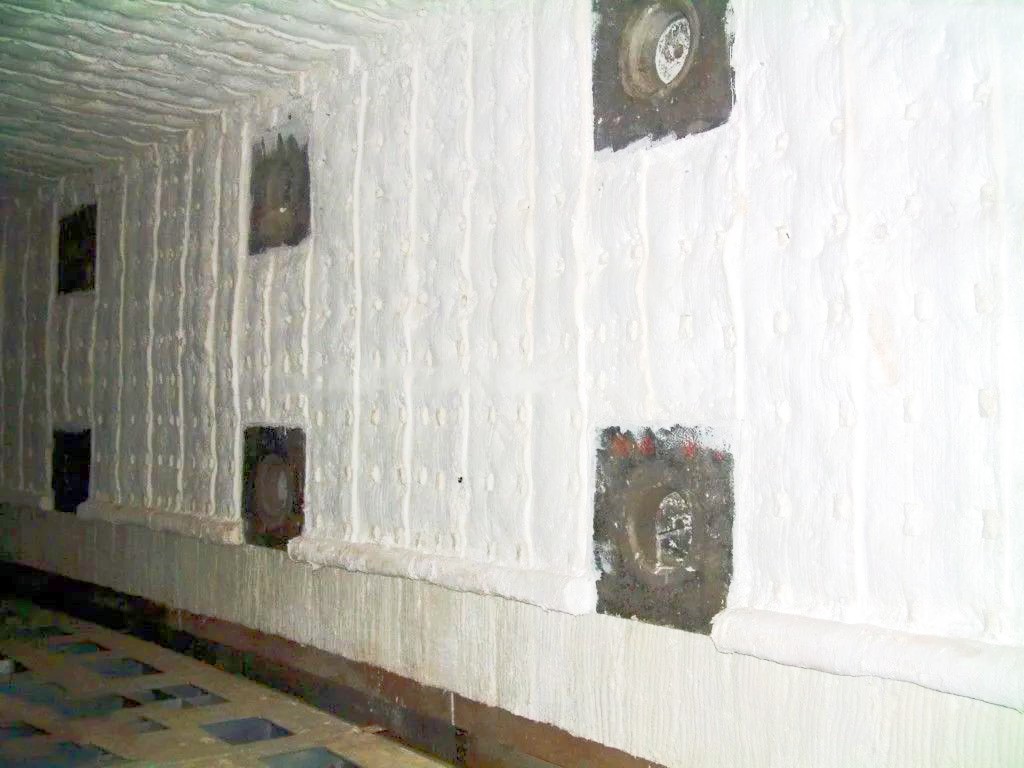
2. Firing Section Operating Temperatures and Insulation Structure
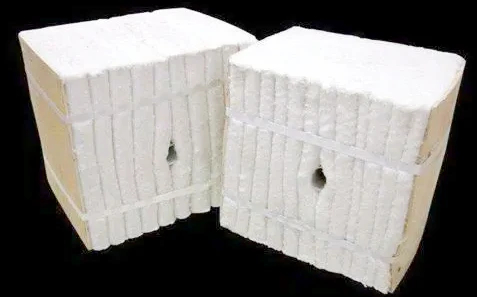
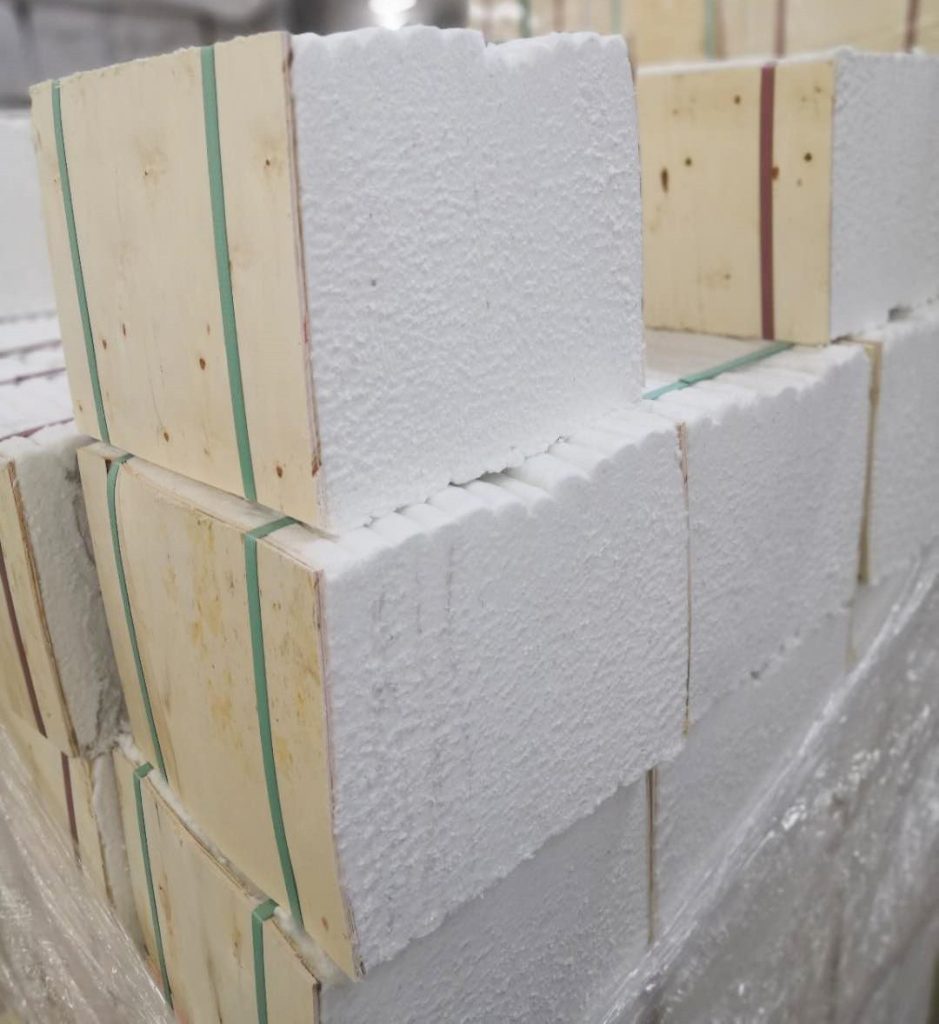
a. Long-term working temperature: 950°C; Theoretical working temperature: 1000°C to 1050°C.
b. High-temperature firing section at 1200°C (calculated based on more severe theoretical conditions): Anchor Company can calculate, taking into account the working temperature inside the furnace, the thickness of the ceramic fiber module on the hot surface, and the total insulation thickness, to determine the temperature reduction on the outer wall of the furnace.
Normal working temperature for the high-temperature section is ≤1050°C. Using high-alumina ceramic fiber modules with a long-term working temperature of 1200°C can meet the requirements for converter operation. As the backup blanket is farther from the hot surface and experiences a greater temperature drop, using ordinary ceramic fiber with a long-term working temperature of 950°C can meet the requirements.
c. Low-temperature section below 650°C: Using ordinary ceramic fiber with a long-term working temperature of 950°C can meet the requirements.
3. Advantages of Using Ceramic Fiber as Lining Material
a. Low bulk density: Ceramic fiber linings are over 75% lighter than lightweight refractory brick linings and 90% to 95% lighter than lightweight castable linings. Using fiber linings can significantly reduce the structural load of the kiln and extend its service life.
b. Low heat capacity (heat storage): The heat capacity of ceramic fiber is only about 1/10 of lightweight heat-resistant linings and lightweight castable linings. The heat capacity of lining material is directly proportional to its weight.
c. Low thermal conductivity: The thermal conductivity of ceramic fiber linings is about 1/10 of lightweight heat-resistant linings, providing excellent insulation.
d. Easy construction: No need to set expansion joints during construction, and workers can be deployed with basic training.
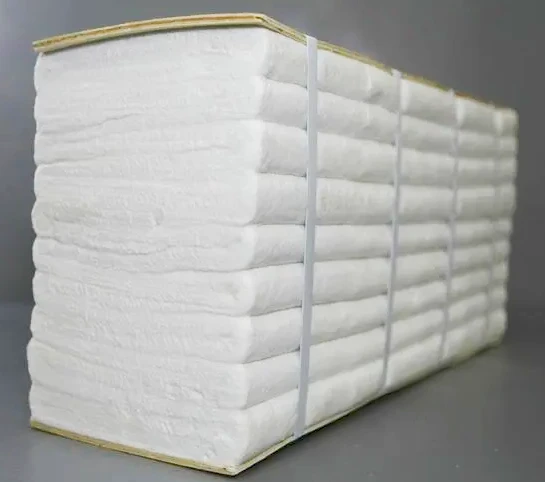
e. Excellent resistance to thermal and mechanical shock: Fiber blankets and modules are flexible and elastic. Given proper heating conditions, fiber fold module linings can be heated or cooled at any speed without easily breaking.
f. No need for preheating: The lining can be put into use immediately after construction, without the need for a preheating process.
g. Good sound insulation: Ceramic fiber reduces high-frequency noise below 1000 Hz. For sound waves below 300 Hz, it outperforms common sound insulation materials, significantly reducing noise pollution.
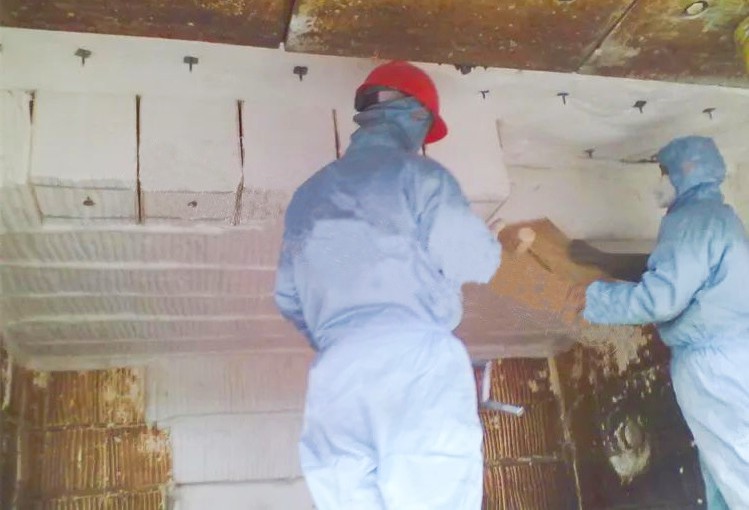
h. Stable chemical properties: Ceramic alumina-silicate fibers are neutral to slightly acidic. They are not eroded by weak acids, alkalis, water, oil, or steam, and are non-wetting by lead, aluminum, and copper.